- Joined
- Apr 11, 2015
- Messages
- 92
- Points
- 103

Hello everyone, I signed up on this forum many years ago but did not visit it much. I took a break from ship modelling, and over the years, the forum which I used to frequent appears to be a ghost town with many of its members migrated here. So I thought that I would migrate my build log to this forum. Please be patient as I rebuild this build log, it will take me quite a while because I started on this kit in 2014 (!!!) and have been working on it intermittently ever since.
From Wikipedia: "HMS Prince was rebuilt by Robert Lee at Chatham Dockyard in 1692, and renamed at the same time as HMS Royal William. During the War of the Grand Alliance the ship saw action at the Battle of Barfleur of 19 May 1692.[5] Prince belonged to the red squadron and carried the flag of Rear-admiral of the red Sir Cloudesley Shovell. She was the first ship to break the French line during the battle.
Later she was rebuilt for a second time by John Naish of Portsmouth but using Chatham Dockyard from 1714, relaunching on 3 September 1719. She was laid up after her re-launch and saw no service at all until she was reduced to an 84-gun Second rate ship in 1756"
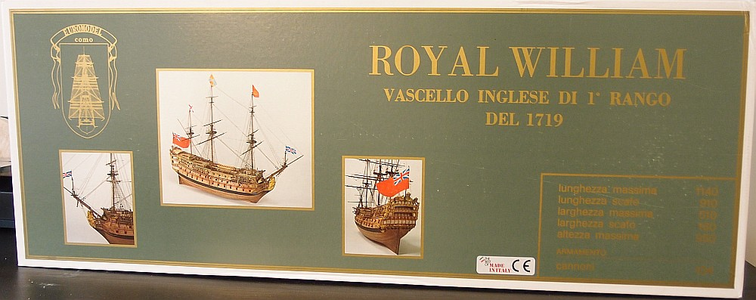
The box is really large and heavy, and arrives absolutely packed. Every bit of spare space is taken up by ... peanut foam. I filled up a plastic bag full of these annoying things and was able to get at the kit.
First, the bad:
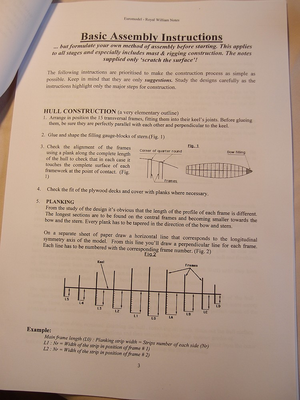
The instructions are not very good (to say the least). For a kit of this complexity, the rather thin instruction booklet only contains THREE pages of instructions, of which the first page is taken up by the history of the ship, and some congratulatory notes. This shot is of the second page, and contains nothing that no experienced modeller wouldn't know. OTOH the plans (see next post) are excellent, however many diagrams in the plans could have been printed on smaller pieces of paper and bound in a booklet instead.
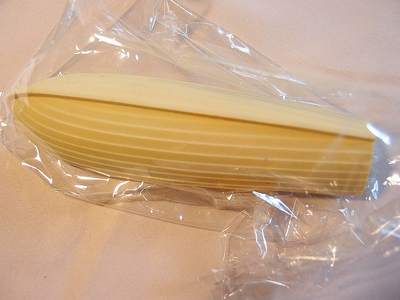
The ships boat is a cast resin item. Whilst it is well cast, other kit manufacturers are offering plank-on-frame boats. Oh yes, only one boat? For a first rate ship?
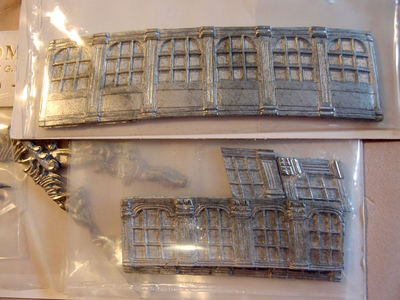
Some of the castings are not very good. Look at how chunky this window is. These will have to go into the bin.
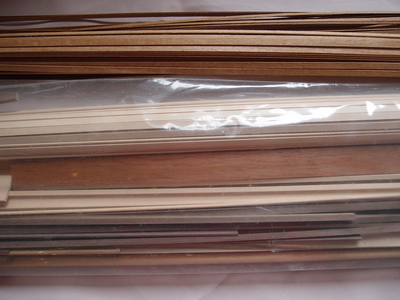
However, the wood is of decent quality. On some older RW kits, the masts are pre-tapered. On this brand new RW kit, fresh from Italy, the masts are not. I ended up replacing most of the wood with pear and holly that I ordered from Hobbymill before they closed.
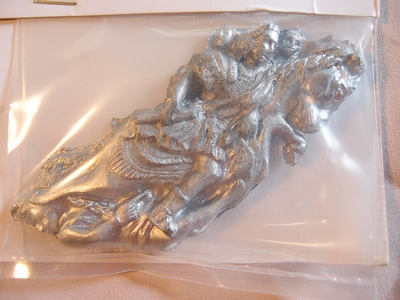
Some other castings, like the figurehead, are excellent.
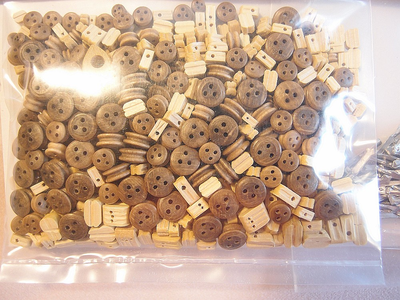
The blocks are probably the best I have ever seen included in a model kit.
From Wikipedia: "HMS Prince was rebuilt by Robert Lee at Chatham Dockyard in 1692, and renamed at the same time as HMS Royal William. During the War of the Grand Alliance the ship saw action at the Battle of Barfleur of 19 May 1692.[5] Prince belonged to the red squadron and carried the flag of Rear-admiral of the red Sir Cloudesley Shovell. She was the first ship to break the French line during the battle.
Later she was rebuilt for a second time by John Naish of Portsmouth but using Chatham Dockyard from 1714, relaunching on 3 September 1719. She was laid up after her re-launch and saw no service at all until she was reduced to an 84-gun Second rate ship in 1756"
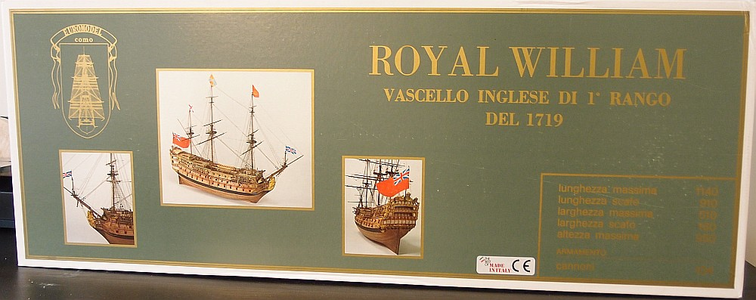
The box is really large and heavy, and arrives absolutely packed. Every bit of spare space is taken up by ... peanut foam. I filled up a plastic bag full of these annoying things and was able to get at the kit.
First, the bad:
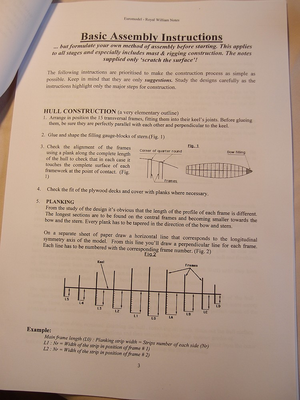
The instructions are not very good (to say the least). For a kit of this complexity, the rather thin instruction booklet only contains THREE pages of instructions, of which the first page is taken up by the history of the ship, and some congratulatory notes. This shot is of the second page, and contains nothing that no experienced modeller wouldn't know. OTOH the plans (see next post) are excellent, however many diagrams in the plans could have been printed on smaller pieces of paper and bound in a booklet instead.
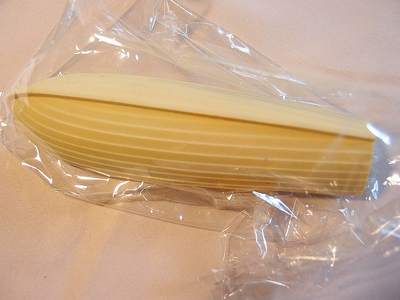
The ships boat is a cast resin item. Whilst it is well cast, other kit manufacturers are offering plank-on-frame boats. Oh yes, only one boat? For a first rate ship?
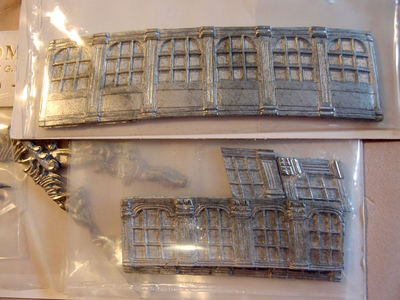
Some of the castings are not very good. Look at how chunky this window is. These will have to go into the bin.
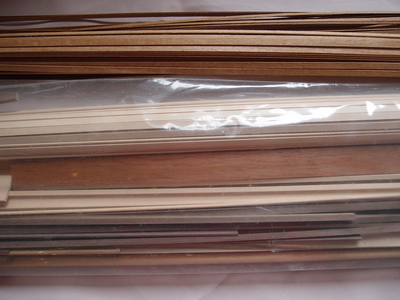
However, the wood is of decent quality. On some older RW kits, the masts are pre-tapered. On this brand new RW kit, fresh from Italy, the masts are not. I ended up replacing most of the wood with pear and holly that I ordered from Hobbymill before they closed.
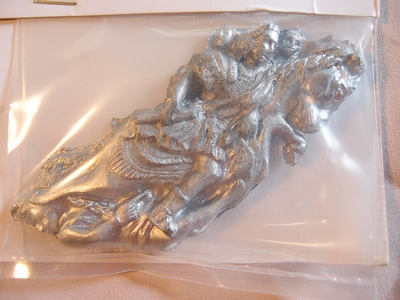
Some other castings, like the figurehead, are excellent.
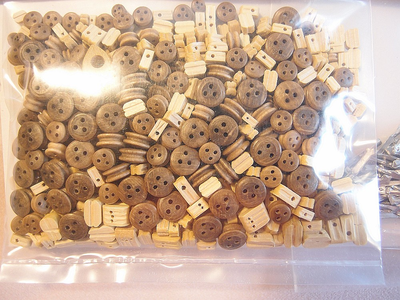
The blocks are probably the best I have ever seen included in a model kit.