The final step in the construction of the stern section of the hull is placing the last frames. In larger hulls these frames are canted towards the stern, in the Alvin Clark’s hull these frames were set square to the keel. Like the half frames in the mid section of the hull, the stern frames are also made in pairs just like the forward cant frames. The last four sets of frames are cut larger than the actual size of the frame to allow for beveling the inside and outside edges.
Some builders would rather pre shape the inside bevels before installing the frames into the hull. This is a matter of builder’s choice. Personally I like to install the full frame blank and shape the frames once they are set in the hull by using various types of sanding disks.
Setting up to install the stern frames is the same as we did for the rest of the hull. First temporally clamp the waterway in place,
With the waterways in place it’s just a matter of hanging the frames in their notches. Notice the frames rise at the foot as they approach the last fashion timber.
Be sure the frame is high enough in the waterway notch so the frame fits tight to the bottom of the waterway like the frame on the right the frame on the left side needs to be pushed up .
Clamping the foot of the frames to the deadwood can be a problem. One way I solved this is to use a square steel block I have. This block is 1 x 2 x 3 and comes in handy for many little tasks. In the photo I wrapped a piece of white paper around the block to clearly show the contact point at the frame. In different areas of the model I will use different glues, in this case I used a 5 minute epoxy. You just apply a little epoxy and push the frame until it makes contact with the deadwood. It takes 2 minutes for the epoxy to grab and 5 minutes for it to set. You can move to each frame one right after the other rather than having to wait for a slow setting glue. At this point the hull is still sitting on the glass building plate and the keel is set between the between the wood strips. By applying pressure against the frame with the block the hull stays put.
Once all the frames that fit into the waterway are in place the short frames are set between the frames using filler blocks. The frames that are in the waterway set the shape of the hull, so adding the short frames between these set frames is just a matter of lining up the face of the frames by feel. The entire framing of the hull is now tied together from the last fashion timber all the way to the bow.
symmetry is the key in framing a hull, to a point you can sand the hull to even out high and low spots and shaping up both sides, but you still need a symmetrical structure to start with.
Looking at the hull from the bottom through the glass building plate you can see the stepping of the half frames. The stepping is a great visual guild for setting the frames. You can see that both sides of the hull are equal and the stepping is about the same distance from frame to frame. When the hull is sanded and the bevels are created the frames will flow one to the other.
The hull of any ship is an art form embracing symmetry and the flow of curves one into another and graceful lines of the sheer profie. The planking flows from the stern to the bow in tapering curves. Even a Great lakes working cargo ship has it's beauty.
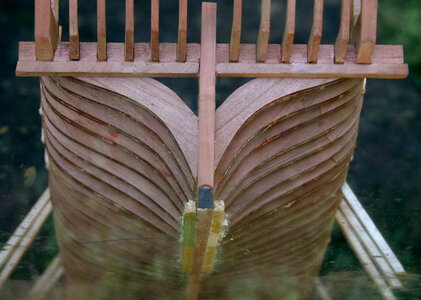