Little things:
Time for an update although it’s just a few time consuming little things for this post. I have gone over to the dark side more and more as my build progresses by using pear wood instead of the supplied kit basswood
. It means though that I am spending a lot of time kit bashing by making parts from scratch.
I made most of the parts for the bilge pump, including the base, from pear and some brass rod/strip. I stayed with the kit designers manual and plans although some research turned up interesting facts about these types of pumps. As usual there is still some basic clean up and treatment for the pear components to do.
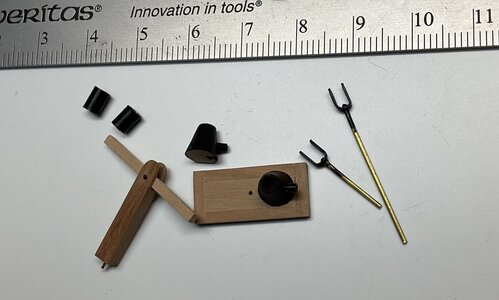
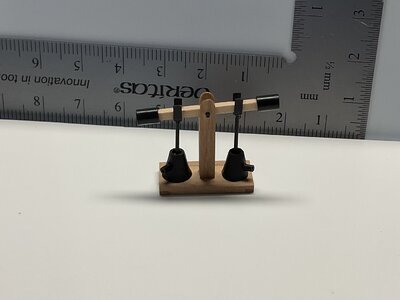
The rudder was set aside for a while but the tiller is just recently made. I added bands to reinforce the tiller arm, much the same as seen in other logs and books. Once again, clean up and final tweaking will be done later on.
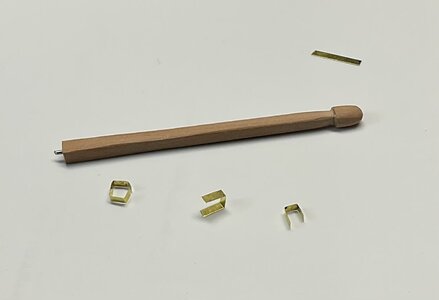
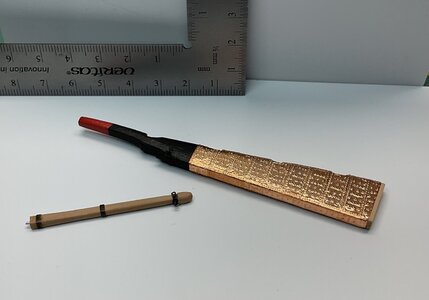
I have also started on the very fiddly headrails. I used pear for the cheeks and hair brackets because the fibrous basswood seems to tear as I indent the moulding profile. In a log by dubz (@Dubz Modelling World) I saw his clever little shop made tool that assists marking out the groove along the cheeks. I made my own using a thin piece of wire and a broken handle. By bending the wire to “close the gap” I can get an approximate mark through the decreasing width of the cheeks. Then a blade and awl provides the gentle depressions for the grooves.
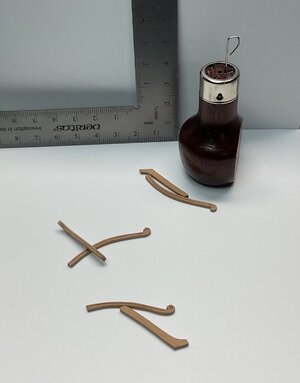
Thanks again for looking in on my log, the support and helpful words and advice mean a lot to me.
Time for an update although it’s just a few time consuming little things for this post. I have gone over to the dark side more and more as my build progresses by using pear wood instead of the supplied kit basswood
I made most of the parts for the bilge pump, including the base, from pear and some brass rod/strip. I stayed with the kit designers manual and plans although some research turned up interesting facts about these types of pumps. As usual there is still some basic clean up and treatment for the pear components to do.
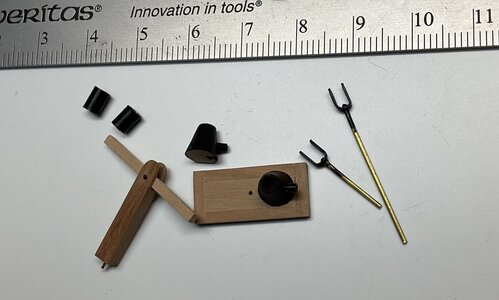
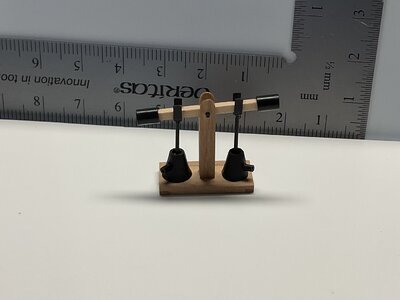
The rudder was set aside for a while but the tiller is just recently made. I added bands to reinforce the tiller arm, much the same as seen in other logs and books. Once again, clean up and final tweaking will be done later on.
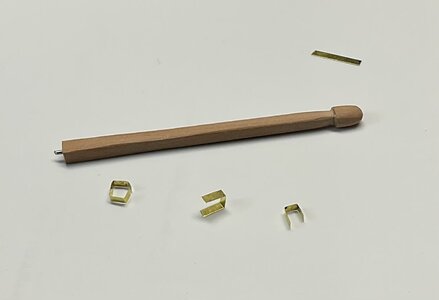
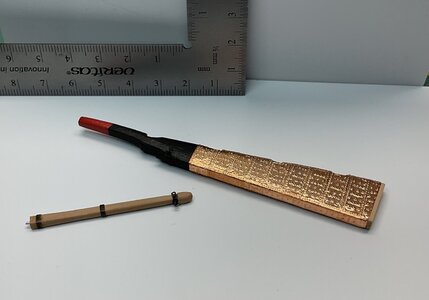
I have also started on the very fiddly headrails. I used pear for the cheeks and hair brackets because the fibrous basswood seems to tear as I indent the moulding profile. In a log by dubz (@Dubz Modelling World) I saw his clever little shop made tool that assists marking out the groove along the cheeks. I made my own using a thin piece of wire and a broken handle. By bending the wire to “close the gap” I can get an approximate mark through the decreasing width of the cheeks. Then a blade and awl provides the gentle depressions for the grooves.
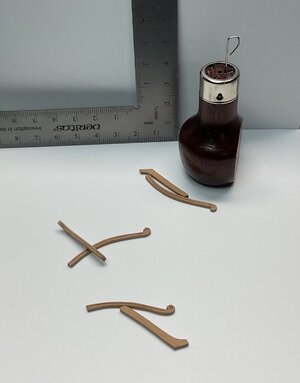
Thanks again for looking in on my log, the support and helpful words and advice mean a lot to me.
Last edited: