- Joined
- Mar 1, 2023
- Messages
- 107
- Points
- 213
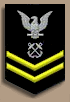
Paul and Ken, thanks for your wise words. I will do my best to keep them firmly in mind in the future.
Not much progress, as shortly after my last post, I managed to cut my thumb while working on La Salamandre. I needed maybe half a dozen stitches (in truth I am not sure how many as I couldn’t bear to look). When I explained how I did it, the doctor gave me the haemostat and two tweezers he used on me as a consolation prize of sorts and told me not to do it again. Apparently, they just throw the instruments away after one use. I think they’ll be really useful. One pair of tweezers has the usual corrugated jaws but the other has U shaped piece on the tip for trapping thread and could be useful for rigging.
Here she is minus the hawse pieces:
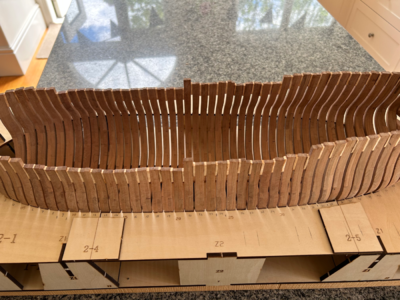
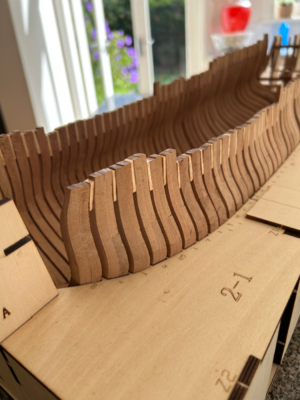
La Salamandre is feeling a bit more like a ship. It’s taken a while to reach this point but, all things considered, things have gone relatively smoothly. That’s not to say there have been periods where I have been quite anxious - e.g. gluing the frames and keelson and filler blocks in particular - but I seem to have been able to work through the issues. I have been assuming the plans are right and I am wrong and have been loathe to start modifying bits to make them fit. This approach, coupled with regular visits to Uwek’s log and Boudroit and Berti, have kept me on the straight and narrow.
Not much progress, as shortly after my last post, I managed to cut my thumb while working on La Salamandre. I needed maybe half a dozen stitches (in truth I am not sure how many as I couldn’t bear to look). When I explained how I did it, the doctor gave me the haemostat and two tweezers he used on me as a consolation prize of sorts and told me not to do it again. Apparently, they just throw the instruments away after one use. I think they’ll be really useful. One pair of tweezers has the usual corrugated jaws but the other has U shaped piece on the tip for trapping thread and could be useful for rigging.
Here she is minus the hawse pieces:
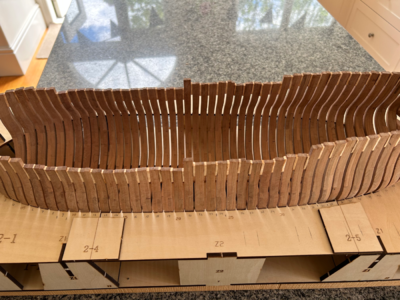
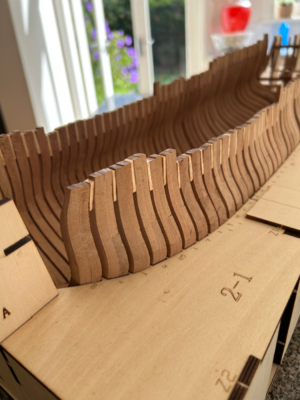
La Salamandre is feeling a bit more like a ship. It’s taken a while to reach this point but, all things considered, things have gone relatively smoothly. That’s not to say there have been periods where I have been quite anxious - e.g. gluing the frames and keelson and filler blocks in particular - but I seem to have been able to work through the issues. I have been assuming the plans are right and I am wrong and have been loathe to start modifying bits to make them fit. This approach, coupled with regular visits to Uwek’s log and Boudroit and Berti, have kept me on the straight and narrow.