If nothing else, I'm sure this thread will supply some laughs. But still, it's an idea.
I am building the Ragusian Carrack by MarisStella, watching Olha's videos, etc., and she show, and everyone suggests, gluing a lot of support blocks between bulkheads to help support and glue planking (single planking in particular), and especially around large changes in curvature like the bow and stern. Modelers have used all kinds of wood for this, usually soft wood, and I've read about people using balsa as well. I think I remember someone saying sheet foam could be used, although that might be more wishful thinking.
Anyhow, I wonder about the possibility of using Great Stuff expanding foam (considered a low expansion foam) to fill the areas between the bulkheads. Yeah, I'm serious. I know, I know, quit laughing and pay attention.
Great stuff sticks to things very well (like members of a built-up hull), can be easily cut and sanded, even painted and filled. Using on a hull such as this:
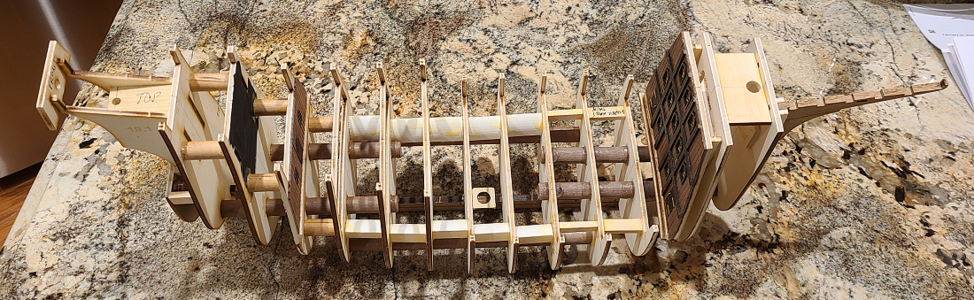
it would fill many nooks and crannies (probably too much, so I may have to block off some areas to prevent it from going there), attach itself really well. Hopefully, careful filling would result in it standing proud of the bulkheads, and then that material could be easily cut off. My son has an electric wire foam cutter which would work quickly and more smoothly than sanding or using a Dremel and with less mess. Of course, final shaping would have to be by sanding.
Foam core wings and such are used for RC airplanes, and when covered with a thin wood or plywood are extremely strong. This method, I think, would actually help stiffen the hull and make it very strong, especially once covered with 1.5mm walnut strip planking.
Yeah, I know I've come up with this idea because I'm lazy. The idea of measuring and cutting numerous wood blocks to fit into the hull, then shape them all, does not sound like fun. And I know there isn't always an easy way out, but was wondering if anyone thinks this has a chance in Hades of working out?
I am building the Ragusian Carrack by MarisStella, watching Olha's videos, etc., and she show, and everyone suggests, gluing a lot of support blocks between bulkheads to help support and glue planking (single planking in particular), and especially around large changes in curvature like the bow and stern. Modelers have used all kinds of wood for this, usually soft wood, and I've read about people using balsa as well. I think I remember someone saying sheet foam could be used, although that might be more wishful thinking.
Anyhow, I wonder about the possibility of using Great Stuff expanding foam (considered a low expansion foam) to fill the areas between the bulkheads. Yeah, I'm serious. I know, I know, quit laughing and pay attention.
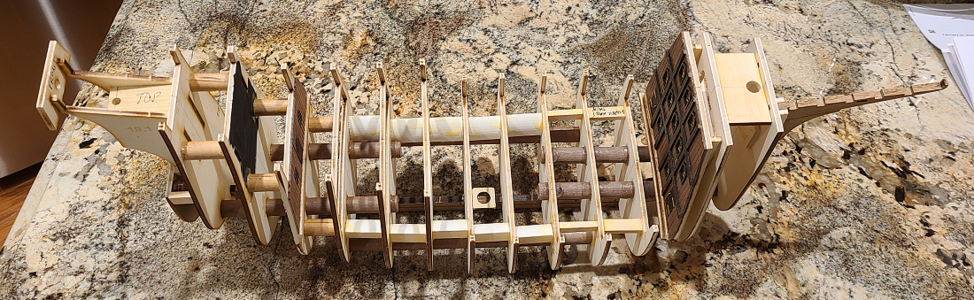
it would fill many nooks and crannies (probably too much, so I may have to block off some areas to prevent it from going there), attach itself really well. Hopefully, careful filling would result in it standing proud of the bulkheads, and then that material could be easily cut off. My son has an electric wire foam cutter which would work quickly and more smoothly than sanding or using a Dremel and with less mess. Of course, final shaping would have to be by sanding.
Foam core wings and such are used for RC airplanes, and when covered with a thin wood or plywood are extremely strong. This method, I think, would actually help stiffen the hull and make it very strong, especially once covered with 1.5mm walnut strip planking.
Yeah, I know I've come up with this idea because I'm lazy. The idea of measuring and cutting numerous wood blocks to fit into the hull, then shape them all, does not sound like fun. And I know there isn't always an easy way out, but was wondering if anyone thinks this has a chance in Hades of working out?