- Joined
- Jul 24, 2022
- Messages
- 79
- Points
- 78

Thanks Kramer.Jamie the hull looks awesome! But could someone explain to me the drop planks vs. wedges.
Wedges are the simple triangle pieces we use to fill in the gaps. Points on all three corners. Absolutely nothing wrong with using them, but technically not a "correct" ship building technique. When building a "real" ship you want to avoid "pointy" things. Because material tapers to such a sharp point, that point becomes an area that wears out early. So they used blunt ends on their tapers to avoid these pointy things. Again in model building, there is nothing wrong with using them, it's a pretty common practice, and very much seen in many instruction manuals. But just like wanting to use aftermarket ropes, blocks or dead eyes, using a drop plank or a stealer adds a different element of realism. See the image below for a typical wedge.
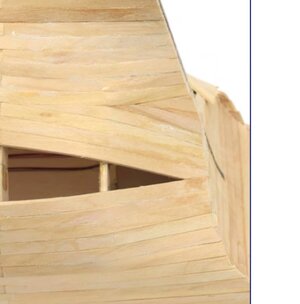
Now, I will try my best to explain drop planks.
Keeping in mind that we want to avoid "pointy" things, take a look a the photo below.
Looking at plank #1, it has a natural flow to the stem. Tapered based on my planking plan.
If you follow plank #2, you will see that the natural flow would end somewhere between the numbers 1&3, resulting in a point, so we "drop" the plank.
I think this means my planking plan was wrong LOL.
The rule of thumb is that the end of the plank should not be less than half the width of the plank. My planks are 5mm wide, so my drop should be no less than 2.5mm.
Now plank 3 would also end in a point (or less than 2.5mm) at the stem so I dropped anther plank.
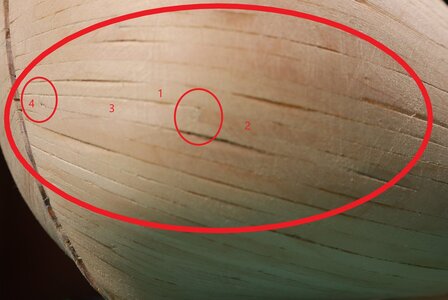
It's a lot of work for a first timer like me, but it was a challenge that I wanted to try. I mean after all, I could just cover it with filler and move on if I failed. It doesn't have to be sea worthy, its just a model my children will toss in the landfill when I'm gone
I hope this answered you question, but if not, let me know and we'll get some real experts in here.
