- Joined
- Jul 26, 2013
- Messages
- 380
- Points
- 158
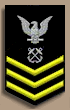
The car is looking great! But my creeping paranoia keeps questioning using latex to skin the body. From bitter personal experience it is NOT archival and will degrade over a few years. Maybe Gerald Wingrove in the Complete Car Modeler might have a suggestion:
secondhand copies are a lot cheaper. Neoprene (common in gloves) might be a better choice- the Museum folks object to it off gassing chlorine, which might not be a problem at home. Here are some latex horror stories:
www.vam.ac.uk
The Complete Car Modeller 1: Wingrove, Gerald A.: 9781861266446: Amazon.com: Books
The Complete Car Modeller 1 [Wingrove, Gerald A.] on Amazon.com. *FREE* shipping on qualifying offers. The Complete Car Modeller 1
www.amazon.com

Disguising Degradation: The Treatment of a Latex Theatre Mask • V&A Blog
by Jacquelyn Peterson-Grace, MS Conservation student, Winterthur/University of Delaware Program in Art Conservation This full-face latex caricature of Edward Heath was part of the Victoria and Albert Museum’s 2018 exhibition Censored! Stage, Screen, Society at 50...
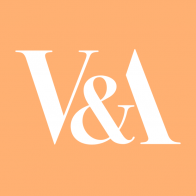
Last edited: