Unboxing
Having just completed the Amati Nina there were no surprises here: a box of good quality materials and fittings. Many of these looked very familiar from my previous build: the windlass, ship's boat, door frames etc. It appears that Columbus bought a job lot when kitting out his fleet. I wonder if he got a discount? Following some shortfalls with the Nina build I took the precaution (while over the free postage threshold!) of appending the kit order with some extra walnut strips with a variety of profiles.
There is a booklet of instructions - unfortunately in Italian - with a condensed English translation. The full scale drawings will probably be sufficient for the build.
The false keel and bulkheads are laser cut from 5mm birch five ply. This will provide a very firm structure on which to build with plenty of contact area for glue between planks and bulkhead and a fair probability of any pins going firmly into their target.
There are thirteen bulkeads which, apart from a few near the ends, are evenly spaced with a mere 30mm pitch. This will define and secure the shape of the hull very well. This is a marked contrast to a similar kit from another manufacturer which uses flimsy 3mm 3 ply. A dry fit of bulkheads and keel was a bit loose so that, after applying glue and squaring up, care was needed to avoid disturbing them before the glue set. I think I must have nudged bulkhead 6 but not so badly that it could not be aligned when planking.
First plank.
If the edges of the bukheads at deck level in a model ship are more-or-less vertical then a starting plank laid here will follow a flat deck. This seems to be a common situation. If the top edges of the bulkheads flare out towards the bow then a plank will tend to curve upwards as it is bent toweards the stem. If the deck also curves upwards then (by luck or design) a starting plank may still follow the deck line. This was the case with Nina.
Santa Maria is perverse! A marked tumble home of the bulwalks means that planks laid here turn down as they are bent towards the stem. The deck curves upwards. No way can a starting plank follow the deck line. Experimenting with a fairly stiff test strip I found that laid 50mm above the bottom of the keel it maintained the same height from stem to stern. This is about the level of the lowest point of the deck midships. I opted to position the starting plank at this height. What will happen above and below I have yet to find out.
The first picture below is a montage of the box, the illustrated instruction book, a plywood sheet (keel and a bulkhead removed) and one of the plan sheets.
Picture 2 isa helpful 1:1 scale plan. Picture 3 is the line chosen for the first plank.
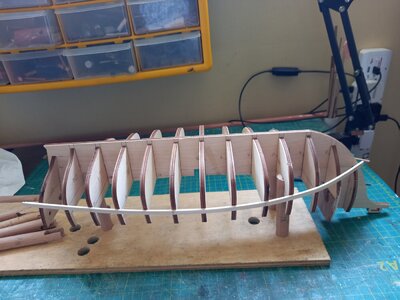
Having just completed the Amati Nina there were no surprises here: a box of good quality materials and fittings. Many of these looked very familiar from my previous build: the windlass, ship's boat, door frames etc. It appears that Columbus bought a job lot when kitting out his fleet. I wonder if he got a discount? Following some shortfalls with the Nina build I took the precaution (while over the free postage threshold!) of appending the kit order with some extra walnut strips with a variety of profiles.
There is a booklet of instructions - unfortunately in Italian - with a condensed English translation. The full scale drawings will probably be sufficient for the build.
The false keel and bulkheads are laser cut from 5mm birch five ply. This will provide a very firm structure on which to build with plenty of contact area for glue between planks and bulkhead and a fair probability of any pins going firmly into their target.
There are thirteen bulkeads which, apart from a few near the ends, are evenly spaced with a mere 30mm pitch. This will define and secure the shape of the hull very well. This is a marked contrast to a similar kit from another manufacturer which uses flimsy 3mm 3 ply. A dry fit of bulkheads and keel was a bit loose so that, after applying glue and squaring up, care was needed to avoid disturbing them before the glue set. I think I must have nudged bulkhead 6 but not so badly that it could not be aligned when planking.
First plank.
If the edges of the bukheads at deck level in a model ship are more-or-less vertical then a starting plank laid here will follow a flat deck. This seems to be a common situation. If the top edges of the bulkheads flare out towards the bow then a plank will tend to curve upwards as it is bent toweards the stem. If the deck also curves upwards then (by luck or design) a starting plank may still follow the deck line. This was the case with Nina.
Santa Maria is perverse! A marked tumble home of the bulwalks means that planks laid here turn down as they are bent towards the stem. The deck curves upwards. No way can a starting plank follow the deck line. Experimenting with a fairly stiff test strip I found that laid 50mm above the bottom of the keel it maintained the same height from stem to stern. This is about the level of the lowest point of the deck midships. I opted to position the starting plank at this height. What will happen above and below I have yet to find out.
The first picture below is a montage of the box, the illustrated instruction book, a plywood sheet (keel and a bulkhead removed) and one of the plan sheets.
Picture 2 isa helpful 1:1 scale plan. Picture 3 is the line chosen for the first plank.
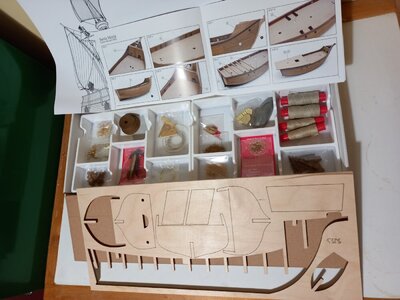
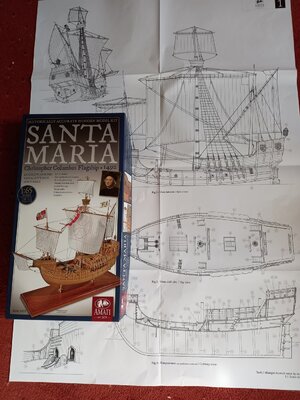
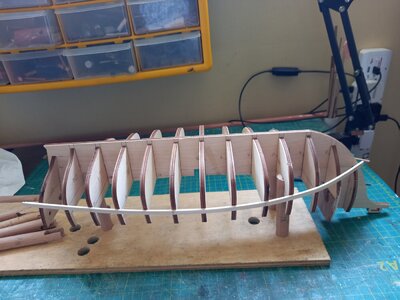