- Joined
- Oct 15, 2017
- Messages
- 986
- Points
- 403
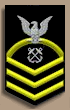
Thank you all.

As to the decorative elements, I have more work to do. To your point, there are a LOT of carvings on the stern of the ship. The photo of Le Fleuron's stern/galleries is a grand example. Note the underlying wood is a lighter version of Pear, so the contrast is not that great between it and the carvings planking underneath. I should state now, I'm either going to keep that planking with the same Pear I used in the stem OR use Black Hornbeam, which I would tie (appearance) to the wales and stem, which will have black elements. The contrast shown in the photo you provided is nice. Below are a couple of photos showing too great a contrast for my liking, although they are beautiful examples of talented modelers. I understand this is a choice and beauty is in the eye of the beholder.

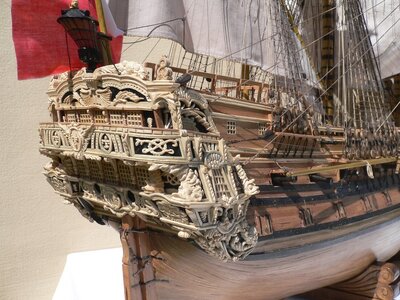
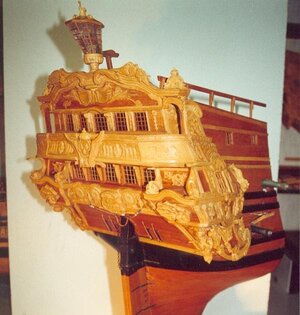
I will do some further testing. Again, as you stated, there is a LOT of decorative carvings on the stern. I want to be sure the Boxwood test piece I used was not representative of all the Boxwood I have in stock. Hoping the wood I do have is of better quality and easier to work with.





This hobby of ours has humbled me in many ways. In good ways.
Thanks Jim. You have a good eye. The Boxwood set of rings IS just slightly wider. The is because I broke 2 sets of rings prior to the finial set you see. So I didn't push sanding them down any further, even with 400grit.WOW!! Looks fabulous. Ken. I like the first one (boxwood), and then pear. However, the boxwood version looks a bit wider, maybe because of the contrast. But boxwood would be my first choice. The real question is will there be more boxwood elements in the stern?
Tobias, thanks. I was hoping for someone to offer alternatives to my first thought/approach. My thought was basically the same as you illustrate, using a board where you use your mill's table and raising it on one end to shave 50% of the piece, then flipping it over and repeating the process. However, I think I will use your method as it is clear now to me it would offer much better control of the stem and more accurate removal of material.Good morning Ken, very nice work. I would agree with Jim and think the boxwood version is the nicest. As Jim has also pointed out the stern of the Le Fleuron has a lot of carving and then it should all fit together.
View attachment 406431
If you have a mill I would use that to taper it. Here is a picture of how I did it for the rudder, for example.
View attachment 406432

As to the decorative elements, I have more work to do. To your point, there are a LOT of carvings on the stern of the ship. The photo of Le Fleuron's stern/galleries is a grand example. Note the underlying wood is a lighter version of Pear, so the contrast is not that great between it and the carvings planking underneath. I should state now, I'm either going to keep that planking with the same Pear I used in the stem OR use Black Hornbeam, which I would tie (appearance) to the wales and stem, which will have black elements. The contrast shown in the photo you provided is nice. Below are a couple of photos showing too great a contrast for my liking, although they are beautiful examples of talented modelers. I understand this is a choice and beauty is in the eye of the beholder.
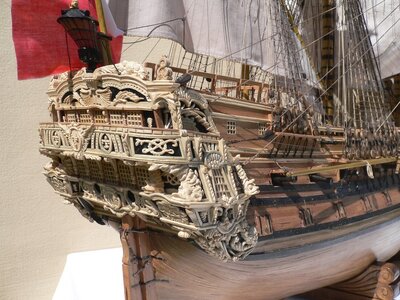
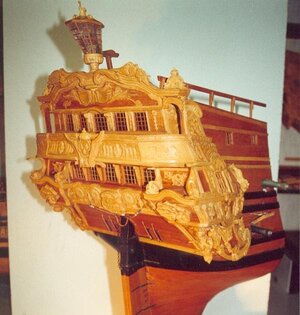
I will do some further testing. Again, as you stated, there is a LOT of decorative carvings on the stern. I want to be sure the Boxwood test piece I used was not representative of all the Boxwood I have in stock. Hoping the wood I do have is of better quality and easier to work with.
Thanks Stephan. I can't even believe you brought up the dog. Don't jinx me!!!wNice update. Looks real good. And keep the dog away.

Thanks Herman. Sometimes I wish I was color blind.Very nice stem. I must confess I am colorblind but I agree, keep the contrast of the rings to a minimum.

Thank you Ken. I've learned so much here on SoS and adopted many sources and methods of those who share. I do try and share my thought process, not just to share back, but to test it with those with much deeper knowledge than I possess. I hope they will point out any existing flaws in my thought process and approach and prevent me from making the mistakes others have who have gone before me. I try and emulate them as much as I can.Hi Ken. That looks very good indeed. I’m impressed with your work and your determination to get it as perfect as you can, also including your thought process within your log adds interest. I wouldn’t even attempt a project as complex, this level of build is beyond me for many reasons but I do enjoy following others in their endeavours. It’s a beautiful subject, perhaps the promised version from Modelship Dockyard could be the way for me to go, I could probably manage Le Fleuron from a kit.

Thank you much Paul. And again for your help with supplier information you were kind enough to share with me!The stem looks fantastic Ken!
Thank you much Roger. I try and share things, as many others do, mostly to show what works and what doesn't, from my perspective, of course. I find sharing my mistakes and how I corrected them have the most value to others. If I can point out a hole, maybe someone else won't twist their ankle!Wonderful work on that stem Ken, I admire your tenacious approach to “getting it right”. I think the other Ken said it well in his prior post. Lots of good how to’s in your log. I also enjoyed reading your rationale for the different methods of caulking too. The graphite and PVA solution is something I’ll put away in my mental filing cabinet.
