- Joined
- Jan 30, 2023
- Messages
- 250
- Points
- 158
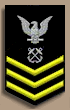
Hello. I will share my patent. Today I accidentally used a grinding drum for a lathe. The 45mm diameter drum does not damage frames and sands flat and rounded surfaces thoroughly. A very interesting solution for grinding. You can precisely adjust the speed, much better than on a drill. You can also rest the frame on the stand. The effect is satisfactory. Slow speed, less noise, easy to clean and grind. I recommend this.
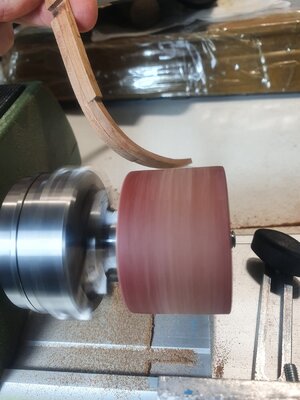
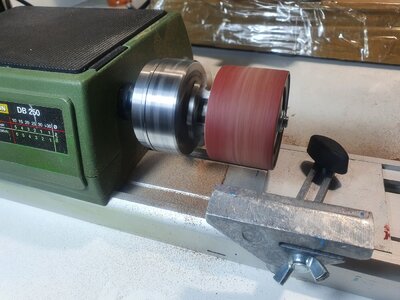
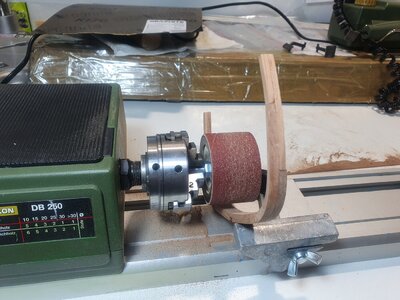
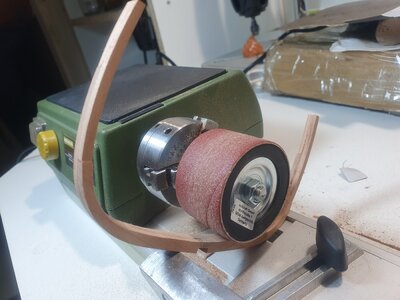
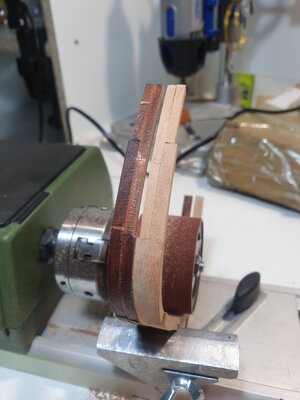
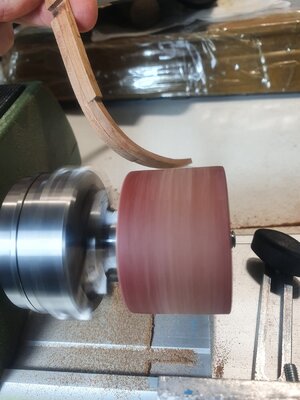
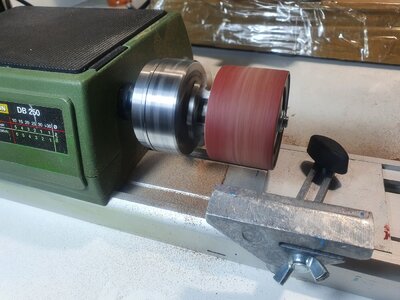
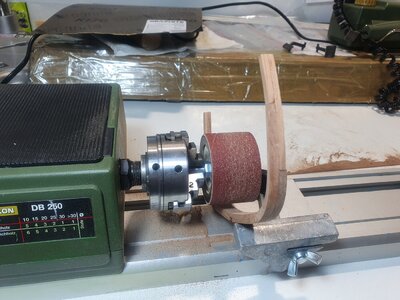
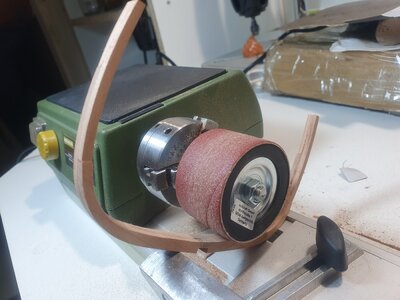
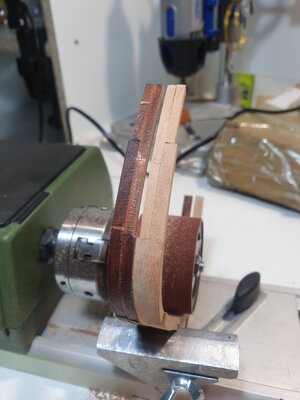