This is a very interesting topic. I do prefer the look of the lap scarf joint rather than the picture frame mitre joint.
On the subject of the lap scarf joint I'm a bit confused on the logic behind the 'dovetail' wedge on some of the below pictured joints, specifically since the lap scarf joint does not have the second dovetail wedge to lock the joint in place.
Also, the lowest point of the wedge is located on the inside of the joint.
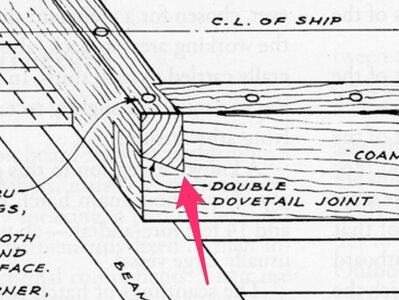
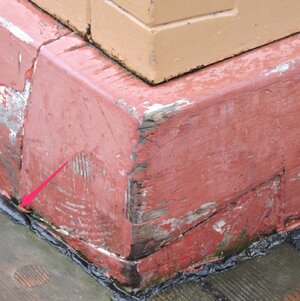
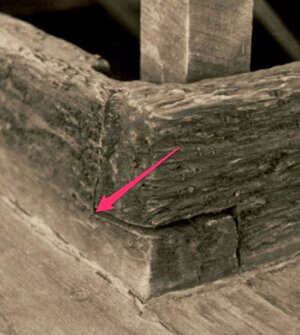
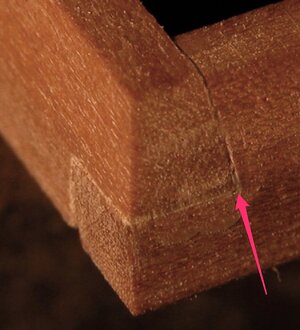
If the lap scarf joint is not serving as a locking dovetail joint, then wouldn't the inner corners of the wedge (red Arrows) be better placed higher than the coaming corner to not allow water to accumulate inside the joint? (I hope I explained this ok)
Or is there another reason for this type of wedge shaped lap scarf joint?
On the subject of the lap scarf joint I'm a bit confused on the logic behind the 'dovetail' wedge on some of the below pictured joints, specifically since the lap scarf joint does not have the second dovetail wedge to lock the joint in place.
Also, the lowest point of the wedge is located on the inside of the joint.
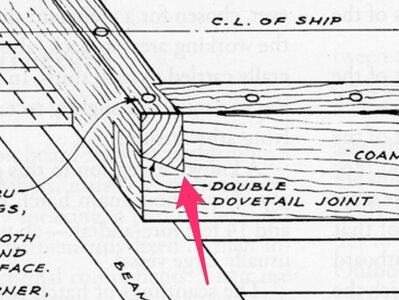
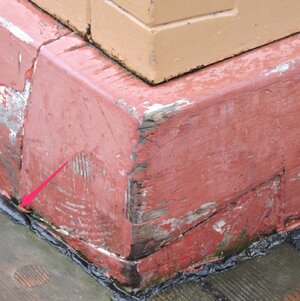
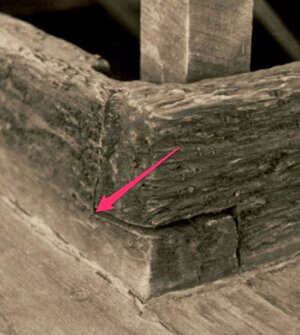
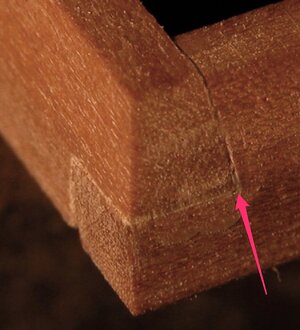
If the lap scarf joint is not serving as a locking dovetail joint, then wouldn't the inner corners of the wedge (red Arrows) be better placed higher than the coaming corner to not allow water to accumulate inside the joint? (I hope I explained this ok)
Or is there another reason for this type of wedge shaped lap scarf joint?