And another thing is sharpening using a leather strop.
The cutting edges will look like a mirror when you sharp in that way. And it makes a difference when you do it like that.
The most important thing to remember is you need a very sharp cutting edge
There are a variety of tools you can use which includes needle files, scalpels, Exacto blades, mini chisels and diamond burs. I use them all.
to start i first cut a blank
then i fit the blank on the model
then using rubber cement i glue the drawing to the blank. The first cut is the back of the lower scroll, an easy cut just make a cut along the pattern and because the grain runs with the scroll it does not take much to cut the depth. The section being cut sits against the upper planks, you could cut away the section up to the back of the scroll then you will have to shape the ends of the planks to match the scroll. Either way works it is just buiders choice.
The scroll is tiny and it looks like a lot of wood to cut away from the front scroll but actually is ia very little
once again i made a stop cut along the pattern and whittled away the material
As you cut the top scroll it is a good idea to check you cutting to make sure you are square looking down on the piece the edge of the scroll is parallel to the leading edge.
looking at it from the front the top of the scroll is even from side to side.
Satisfied with the shape of the top scroll i went in with a needle file and sharpened up where the bottom of the scroll meets the top of the cap rail. Yes that is the end of the file and i just used it in the photo to show what i did.
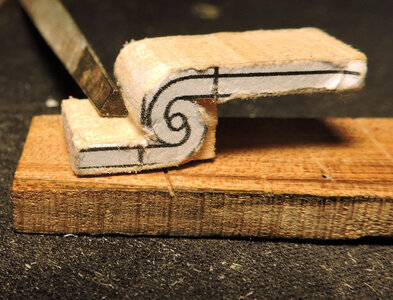