For those of you who are unfamiliar with the 3d resin printing process like I was, I thought it could be interesting to show the different steps requiered to print a part .
1- decide what to print. In this exemple, I wanted to improve the head light protection grill from this
To this
2- 3d model the part
3- load the model in a slicer application. A slicer will literally slice the part in a multitude of layers. The number of layers depent on 2 things, the height of each layer, in this case it's 50 microns (.05mm) and the total height of the print. The taller the print, the more layers will be requiered and the longer the print will take. That's what fun with this process, the printing time is not dictated by the surface area being printed so a single small part of say 3mm height and 10mm square area will take as much time as 'X' of the same part as long as they fit on the printing plate. Now, this is where the game is won or lost. You have to give the proper orientation to the part so as to not have too much surface area being printed on each layer while taking care of the esthetics. You want to avoid supporting the part on visible surfaces because the anchor point will show a bit (or alot depending on their size and number). In this case, I wasn't able to avoid this but fixed the problem later on. Once oriented, you then add supports. The idea is to support the part at strategic point as it's being printed, avoiding overhangs.
View attachment 20231229_071358.mp4
4- load in printer and print
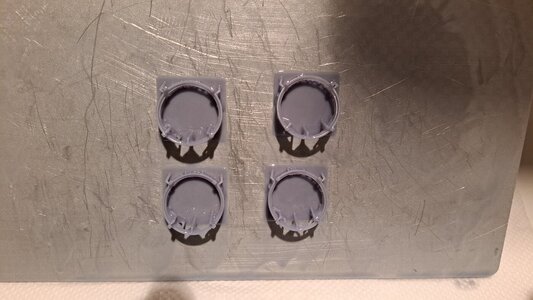
5- wash part in washing station. I use a water wash resin so cleaning is done with water. Most resin will requier cleaning with alcool
6- remove part from support structure by diping in boulingrin water for 2 to 3 seconds. This is not always necessary but will make separation alot easier.
Before boiling
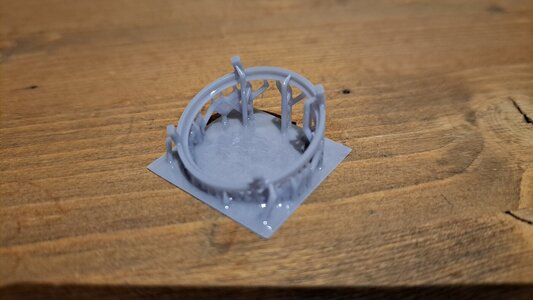
After 2 sec dip
7- Cure in curing station. Most small parts will cure in 2 minutes. The longest I cured à part was 5 minutes. (The washing and curing uses the same machine, at least mine does)
After curing ( notice the bumpy top surface)
8- part finishing. Here you have to remove any anchor points that will be visible with either a blade, snippers or sand paper. I this case, not being able to support the part on a non visible surface ( I tried 5 different orientations but only one worked, I'm sure that someone with more experience could have achieved this), I printed a sanding tool since this part is very fragile.
Sanding tool
And after sanding
All that is left to do is to install the wire mesh
and chrome.
So that's it, hope you enjoyed this!!