Started by building the jig. Mine did not lay flat. I weighted it down to a marble slab, then glued the edge parts on. After drying overnight it was better, but still not flat. one corner wanted to lift up about 1/8". I wanted to build a rotating jig anyway, so I weighted it down again, doubled up the edge parts with some heavier pieces, glued them on and dried overnight. Then I built the base and ends for the rotating part and assembled everything. After I was done, I transferred it to a 3/8" thick glass plate to check for flatness. Now, it's right on dead flat and the base sits flat too, with no wobble.
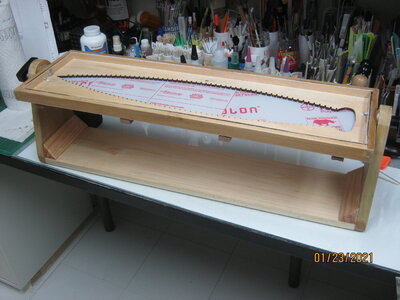
I have done this for plastic ship kits too. One for basic rough work that I can lay on it's side, and one for finishing work, in both 1/350 and 1/700.
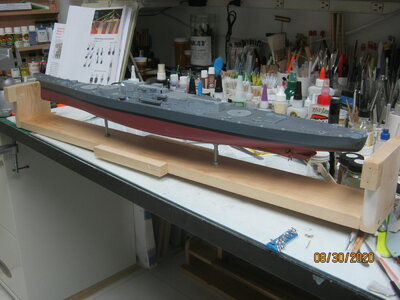
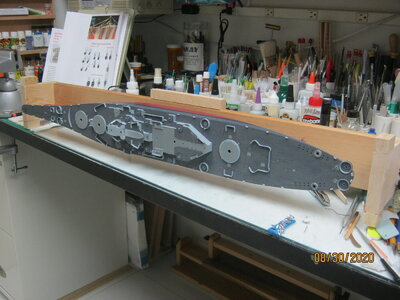
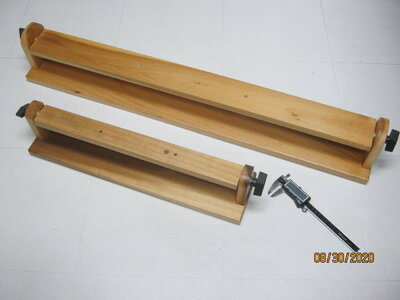
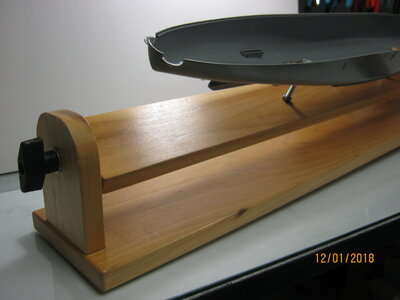
Now, to get on with building all those frames and the keel.
EJ
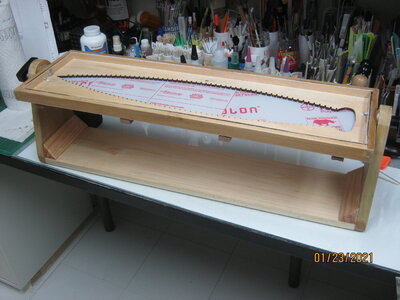
I have done this for plastic ship kits too. One for basic rough work that I can lay on it's side, and one for finishing work, in both 1/350 and 1/700.
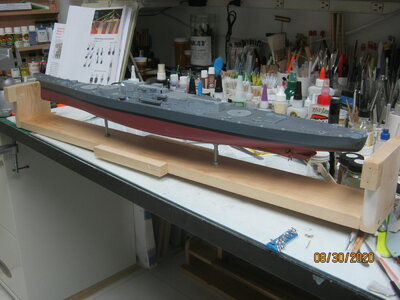
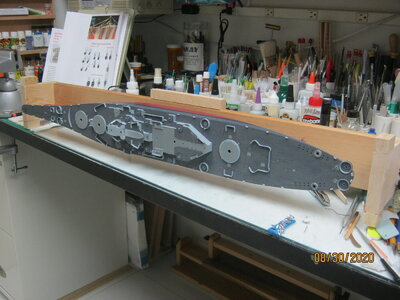
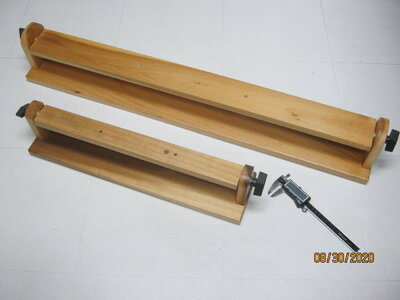
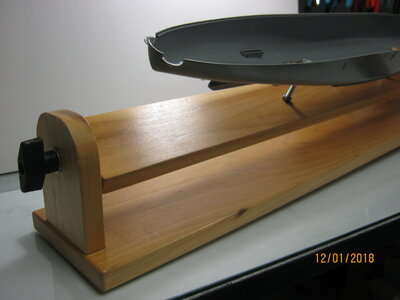
Now, to get on with building all those frames and the keel.
EJ