- Joined
- May 1, 2023
- Messages
- 115
- Points
- 113
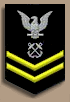
I'm fairly new to CNC machining, and I've been doing it for a little less than a year.
Currently, I'm focusing on improving the precision of fixing the material, which will allow me to work on smaller details.
So far, I have been working on relatively larger projects, like this windlass version (scaled at 1:65).
This is my first attempt at this windlass, and I consider to make some improvements in the future (it's not yet glued into the model).
However, it functions well and was quite easy to assemble.
For modeling, I use Fusion 360.
The main idea behind this project was to create a set of pieces that would eliminate the need for "double-sided" or "flip" CNC processing.
Here are some stages with stages of the process and the final result.
And also the link to a video where I'm assembling it...
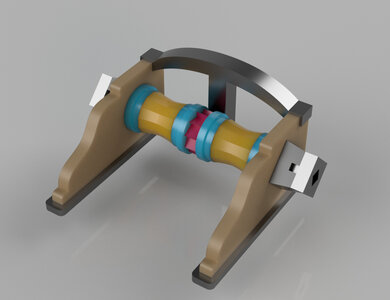
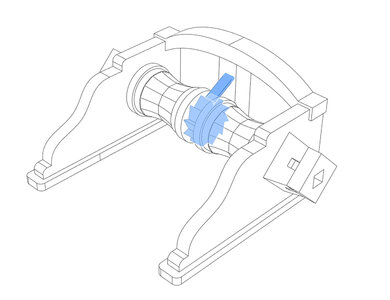
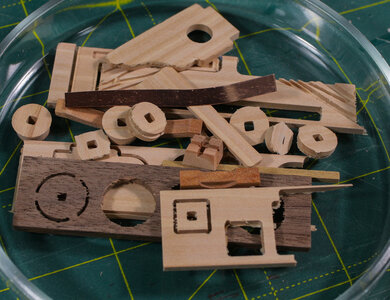
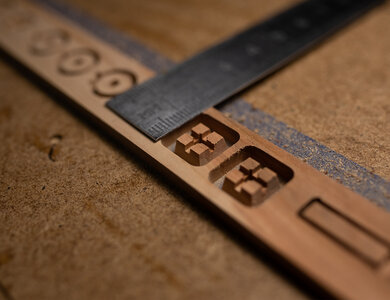
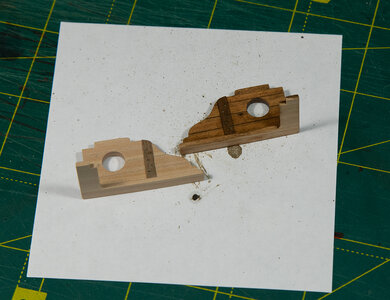
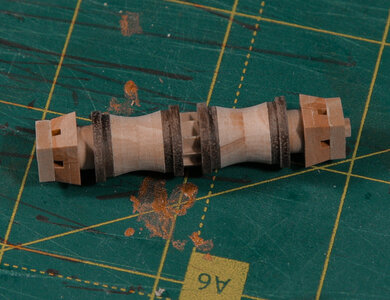
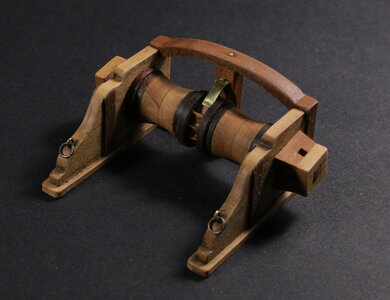
Currently, I'm focusing on improving the precision of fixing the material, which will allow me to work on smaller details.
So far, I have been working on relatively larger projects, like this windlass version (scaled at 1:65).
This is my first attempt at this windlass, and I consider to make some improvements in the future (it's not yet glued into the model).
However, it functions well and was quite easy to assemble.
For modeling, I use Fusion 360.
The main idea behind this project was to create a set of pieces that would eliminate the need for "double-sided" or "flip" CNC processing.
Here are some stages with stages of the process and the final result.
And also the link to a video where I'm assembling it...
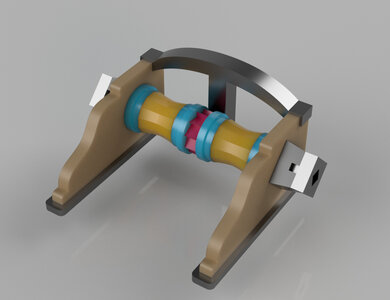
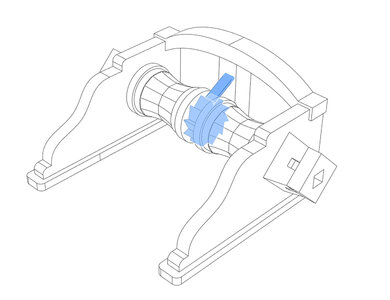
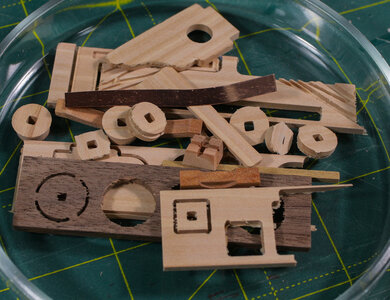
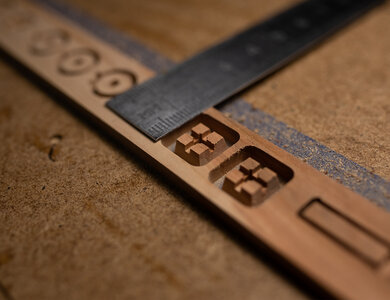
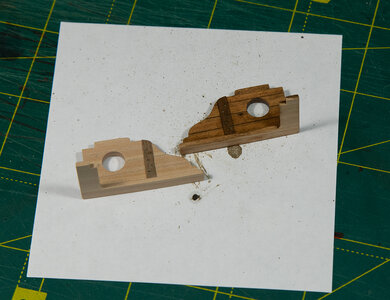
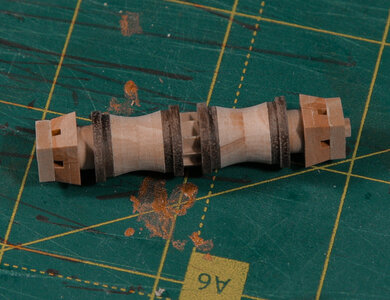
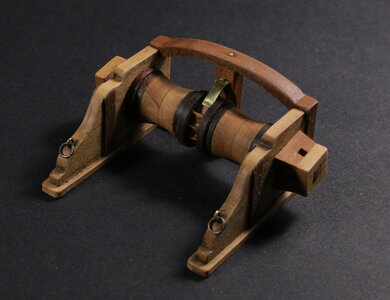