- Joined
- May 1, 2023
- Messages
- 115
- Points
- 113
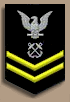
Hi colleagues,
Here, I will share a few words about my CNC machine.
Additionally, I will try to provide the results of my small market research that I conducted while searching for a machine.
There are the machine specifications:
• Working Table: 400mm x 300mm x 135mm
• Clearance: 170mm • Height from table to spindle nut: 220mm.
• Frame: Cast iron
• Ball Screw SFU1605. Taiwan.
• 20mm rail guides. Taiwan.
• Integrated stepper motors on all axes: 2.4 Nm, 200 steps/revolution (1.8 degrees).
• Spindle: 1.5 kW, ER16, water-cooled, 24000 rpm.
• Capability to cut threads of any size using spiral interpolation.
• Spindle activation synchronized with program start, pump, air, and coolant.
• Rapid traverse speed (G0) up to 4000 mm/min.
• Processing accuracy up to 0.01 mm, repeatability not worse than 0.025 mm.
• Non-perpendicularity for X/Y not worse than 0.01 mm over 200 mm, and for X/Z and Y/Z not worse than 0.01 mm over 120 mm travel.
• Machine dimensions: W x D x H: 700mm x 620mm x 650mm.
• Machine weight: 170 kg
The machine is controlled by DDCS v 3.1. I'm not sure this is the best controller ever, but so far I had no problems with it.
What is especially convenient for me - this CNC does not need a PC to be plugged in. The control program (G-code) is transferred via a flash drive.
And this is how it looks:
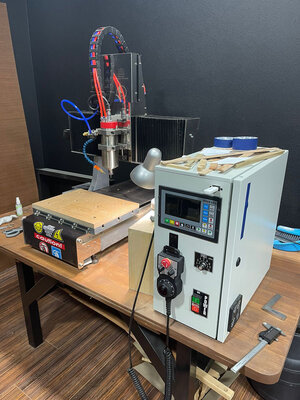
The machine is far not lightweight. 170 kg forced me to design and make a special "heavy-duty" table for it.
The box, light, and vacuum cleaner will follow sometime... Hopefully...
I will continue, if you find this part interesting...
Here, I will share a few words about my CNC machine.
Additionally, I will try to provide the results of my small market research that I conducted while searching for a machine.
There are the machine specifications:
• Working Table: 400mm x 300mm x 135mm
• Clearance: 170mm • Height from table to spindle nut: 220mm.
• Frame: Cast iron
• Ball Screw SFU1605. Taiwan.
• 20mm rail guides. Taiwan.
• Integrated stepper motors on all axes: 2.4 Nm, 200 steps/revolution (1.8 degrees).
• Spindle: 1.5 kW, ER16, water-cooled, 24000 rpm.
• Capability to cut threads of any size using spiral interpolation.
• Spindle activation synchronized with program start, pump, air, and coolant.
• Rapid traverse speed (G0) up to 4000 mm/min.
• Processing accuracy up to 0.01 mm, repeatability not worse than 0.025 mm.
• Non-perpendicularity for X/Y not worse than 0.01 mm over 200 mm, and for X/Z and Y/Z not worse than 0.01 mm over 120 mm travel.
• Machine dimensions: W x D x H: 700mm x 620mm x 650mm.
• Machine weight: 170 kg
The machine is controlled by DDCS v 3.1. I'm not sure this is the best controller ever, but so far I had no problems with it.
What is especially convenient for me - this CNC does not need a PC to be plugged in. The control program (G-code) is transferred via a flash drive.
And this is how it looks:
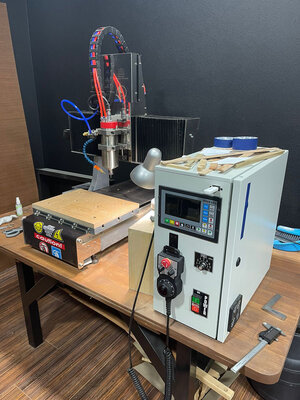
The machine is far not lightweight. 170 kg forced me to design and make a special "heavy-duty" table for it.
The box, light, and vacuum cleaner will follow sometime... Hopefully...
I will continue, if you find this part interesting...