4/16 to 4/19
The balcony railing is up next, and will require 45 degree miter cuts at each corner. The cutting goes smoothly and while doing so I learned something that is pretty helpful about the miter box that I have. Its floor has multiple grooves of varying sizes.
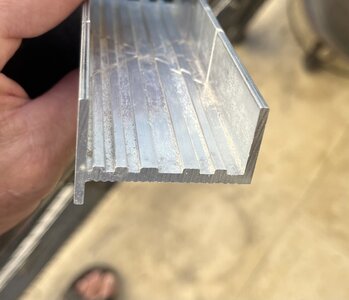
I hadn’t even noticed this before but today I noticed that the grooves matched common board sizes, allowing me to hold the board more securely.
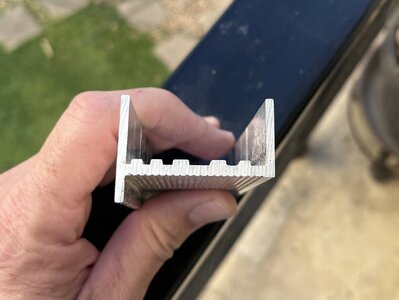
Very cool little unknown feature, at least to me.
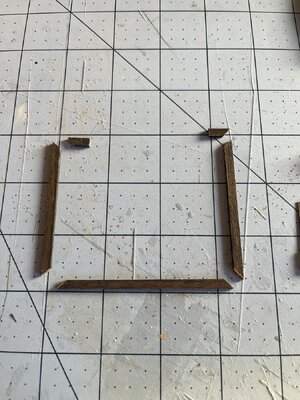
After cutting and sanding the rails, they were glued in place. Once dried, a little sanding and staining and they are looking sweet.

Next up is the rudder which will include 2 things that I have not done before… metal work and using CA glue (super glue).
I had already stained the rudder (when I stained the wood for the balcony railing) but now I notice that I should have marked it off to simulate planks.
At first I tried using my fine saw to cut the 2 grooves and then used a pencil to color them in. The grout lines were barely visible.
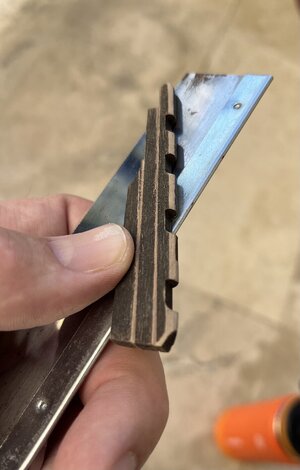
So then I cleaned the grooves up again with the saw and then taped them off and painted them black. Still barely visible.
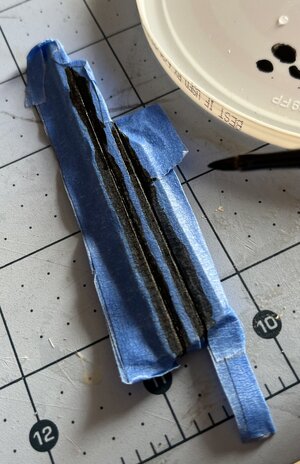
My third attempt was a light sanding followed by using the pencil again followed by touching up the stain. Still barely visible but I’m done trying. It’s as good as it is going to get.
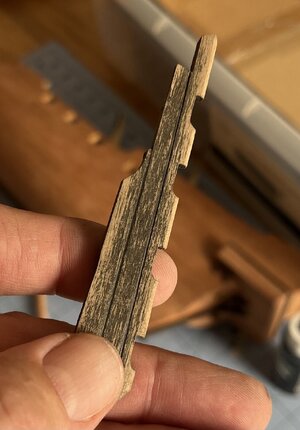
Metal Work and Super Glue - Heads up… the next section is long winded, even for me, so be prepared.
Other than one small part on my Bluenose (a small sheet buffer that is mostly hidden under a wooden platform), the brass hinges will be my first work with metal. Then add the fact I’ll be using super glue for the first time and the rudder is something I’ve definitely been concerned about for a while.
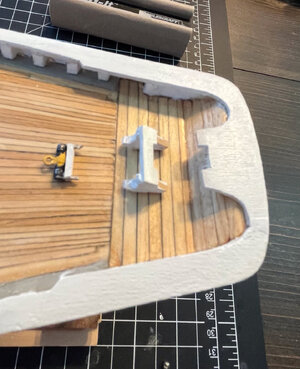
There are 4 hinges, each consisting if 3 pieces. Two small (preformed) strips of brass and then a small piece of brass 3/64” round stock. The hinges all start off looking the exact same, but each of the 8 pieces end up being different. The only thing that stays the same is the round stock. For each hinge, I determine that I need a piece of the round stock about 6mm.
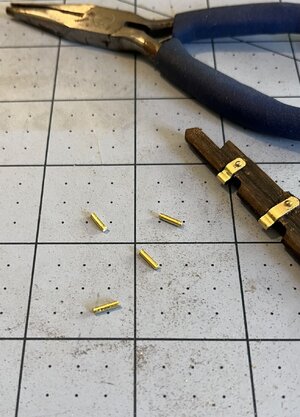
Each hinge will also need either 2 or 4 nails. These nails are cut down so the go into the rudder but not through the rudder.
On the rudder-side of the hinges, the hinges get longer as they get lower on the rudder. The top one gets cut off right about the 1st pre-drilled hole. The cut ends gets sanded to a rounded tip, and then the fun begins.
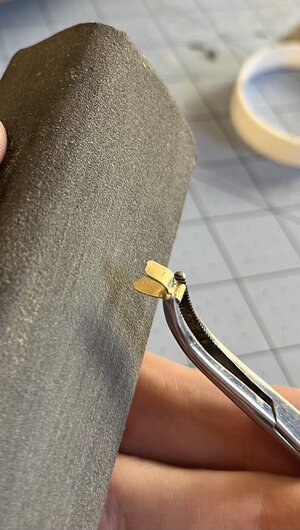
I determine where the nail needs to go on the strip and drill a very tiny hole into the brass. I didn’t measure the diameter of the hole, but ideally you want it just a little bit smaller than diameter of the nail.
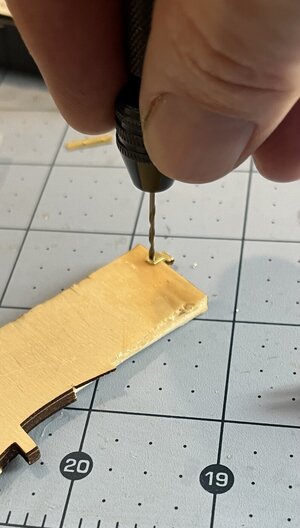
The hinge needs to go over/around the rudder which is 3/16” thick. The round brass stock gets held in the bend or crook of the hinge. So you gently pinch the round stock in crook of the hinge using a small pair of needle nose pliers. Then you form the initial bends in the hinge by pushing it against a scrap piece of 3/16” board. I used a scrap piece of wood to reduce the possibility of breaking the rudder. Gently move the pliers back and forth until the round stock is as close to the edges of board as possible.
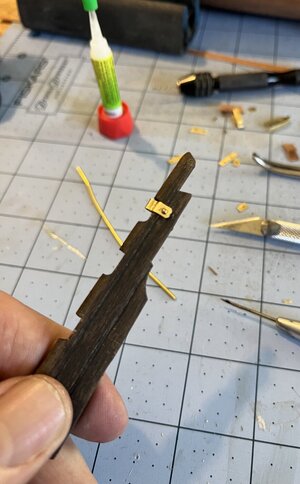
Returning the hinge to the rudder, see if the round stock has been moved close enough to the edge of the rudder. If it sticks out of the cut-out, it needs to be bent a bit more on the scrap board.
Once the hinge has been manipulated to fit correctly, hold it in place and drill a hole into the rudder through the holes you just drilled in the hinge.
Now I get to use super glue for the first time… using a toothpick I add the super glue to the back (or inside) of the hinge. I push it into place and then using a set of hemostats, I hold the hinge against the rudder, leaving access to the hole. I then put a nail into the hole and tap/push it into the rudder. I then add the nail on the other side. I remove the hemostat and gently tap the nail fully down.
One rudder-side hinge down (3 more to go).
It is at this point that I notice the super glue has bleed/ran a bit. Nothing I can do right now. Some quick research shows that I probably need to get some thicker glue plus some applicator tips. I post the question of how to fix this in my build log. More on this later.
The other 3 hull-side hinges went the same except that each one is a little different in length plus they each have 4 nails (2 per side).
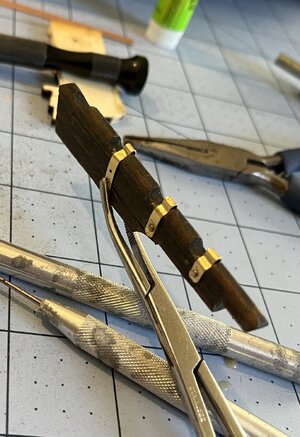
Once all 4 were done, I needed to install the round stock in each one. A little bit of finagling and they were in. A drop of super glue on each one while using the needle nose pliers to hold it in place and the rudder-side hinges are done.
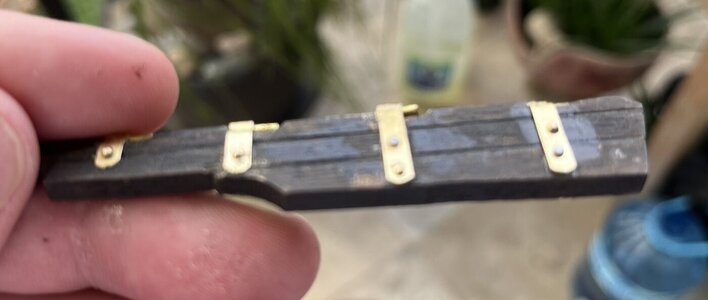
To start the hull-side hinges I held the rudder in place and used a pencil to mark where each hinge needs to be. Three of the four hinges will be the same length. The top most hinge needs to be quite a bit shorter as it’s located right at the gun ports for the chase guns that I added.
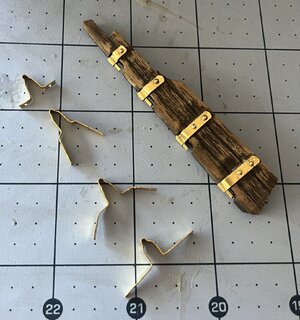
Each hinge varies in shape because of where it will attach to the hull. I bend the ends of each hinge at approximately 5mm from the crook of the hinge to reach from the round stock and then wrap around the 4mm thickness of the sternpost. I then place the hinge at the marks of where each will be and then bend the ends against the hull.
In order to get the correct length of the top most hinge, I needed to put the gunport frame in place. In addition to get the length, I noticed that the inner portions of where I had widened the gun ports out were still very noticeable since the center of each dummy gunport was painted black. The outer edge was fine as I had painted them to match the hull. So I took this break (while waiting for any recommendations/answers on my posted super glue question) and painted the sides of all of the gun ports black plus touched up the back of the dummy gun ports.
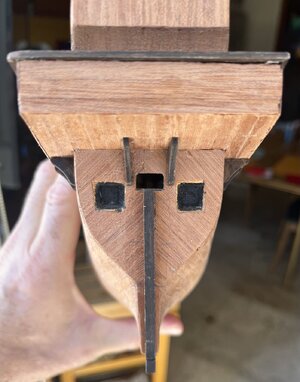
The super glue bleed issue… Surprisingly no one offered any advice when I posted the question earlier in the day other than a couple of “likes” which I will assume was to my “maybe sanding?” as the fix. So I did some sanding and touched up the stain.
I slide the 4 pre-bent hull-side hinges through the opening between the round stock and the rudder, keeping the shape as much as possible. Using hemostats, I gently pinched the hinges around the round stock. While keeping the hemostats attached to the hinge, I used the needle nose pliers to open up the hinge so it will slide over the stern post.
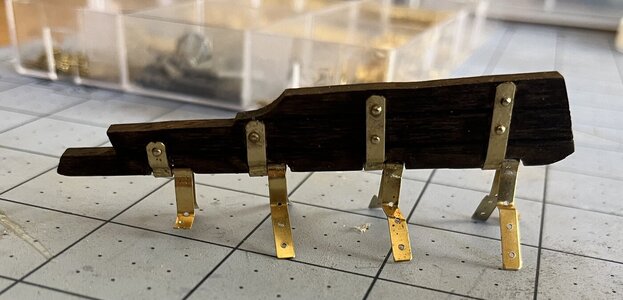
After aligning the hinges with the marks that I had previously made, I slowly pushed in the nails in every pre-drilled hole. Given my previous problems using super glue, I only used the nails to hold the hinges in place. I know I’m taking a risk with them falling out over time, but my thought is to buy thicker glue and tips in the States and add it after the fact.
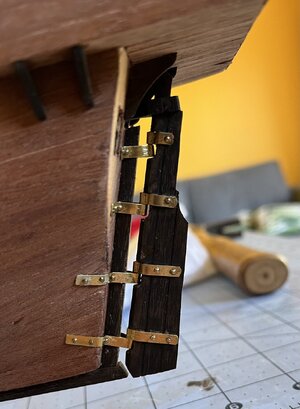
All in all, the hull-side hinges were a lot easier than I expected.
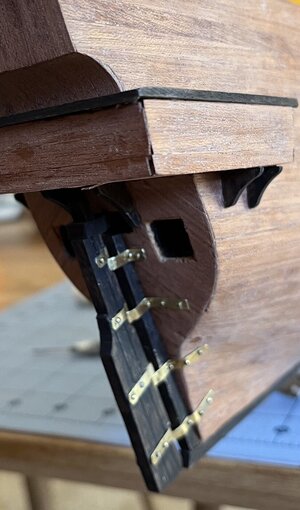
Time for this portion: 5 hours
Total time to date: 124.5 hours