- Joined
- Apr 2, 2021
- Messages
- 184
- Points
- 113
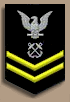
Wasn’t JESUS A carpenter?I know this store!!
View attachment 407397
View attachment 407401
here is the virtual tour.
Baptist
www.google.com
Wasn’t JESUS A carpenter?I know this store!!
View attachment 407397
View attachment 407401
here is the virtual tour.
Baptist
www.google.com
it is suggested that waterproof sandpaper better works while wet.nteresting. Which is better, waterproof black or regular red? They are the same... Here the gradation is 80.
In my opinion, it's a poof to pay more.
...he was a carpenter as well.Wasn’t JESUS A carpenter?
Thank you for this post, very interesting indeed.I see an interest in the thread, and I want to thank you all who participated. But... how many of us actually know what is the sandpaper made of and how to choose the correct one for a given job? Stay tuned and you will have a chance to learn, thanks to WIKI!!
Sandpaper, also known as glasspaper, is a heavy paper with abrasive material bonded to its surface. Sandpaper is part of the "coated abrasives" family of abrasive products. It is used to remove small amounts of material from surfaces, either to make them smoother (painting and wood finishing), to remove a layer of material (e.g. old paint), or sometimes to make the surface rougher (e.g. as a preparation to gluing).
The first recorded instance of sandpaper was in 13th-century China when crushed shells, seeds, and sand were bonded to parchment using natural gum. Sharkskin was also used as a sandpaper. The rough scales of the living fossil Coelacanth are used by the natives of Comoros as sandpaper. Boiled and dried, the rough horsetail is used in Japan as a traditional polishing material, finer than sandpaper.
Sandpaper was originally known as glass paper, as it used particles of glass. Glass frit has sharp-edged particles and cuts well, sand grains are smoothed down and do not work well like sandpaper made from glass. Cheap counterfeit sandpaper has long been passed off as true glass paper; Stalker and Parker cautioned against it in the 17th century. Glass paper was manufactured by John Oakey's company in London by 1833, who had developed new adhesive techniques and processes, enabling mass production. A process for making sandpaper was patented in the United States on June 14, 1834, by Isaac Fischer, Jr., of Springfield, Vermont.
In 1921, 3M invented a sandpaper with a waterproof backing, known as Wetordry. This allowed use with water, which would serve as a lubricant to carry away particles that would otherwise clog the grit. Its first application was automotive paint refinishing.
Material Materials used for the abrading particles are:
Sandpaper may be "stearated" where a dry lubricant is loaded to the abrasive. Stearated papers are useful in sanding coats of finish and paint as the stearate "soap" prevents clogging and increases the useful life of the sandpaper. The harder the grit material, the easier the sanding of surfaces like wood. The grit material for polishing granite slab must be harder than granite. Later abrading surfaces include long-life stainless steel sanding discs. Sandpapers can also be open coat, where the particles are separated from each other and the sandpaper is more flexible. This helps prevent clogging of the sandpaper. The wet and dry sandpaper is best used when wet.
- Flint: no longer commonly used
- Garnet: commonly used in woodworking
- Emery: commonly used to abrade or polish metal
- Aluminum oxide: perhaps most common in the widest variety of grits; can be used on metal (i.e. body shops) or wood
- Silicon carbide: available in very coarse grits all the way through to microgrids, common in wet applications
- Alumina-zirconia: (an aluminium oxide–zirconium oxide alloy), used for machine grinding applications
- Chromium oxide: used in extremely fine micron grit (micrometer level) papers
- Ceramic aluminum oxide: used in high-pressure applications, used in both coated abrasives, as well as in bonded abrasives.
View attachment 407726
View attachment 407727
Thank you and enjoy
As always Jim, great stuff. I never get tired of learning. Thanks for sharing! You've also reminded me of something I needed to test, but forgot all about. For wood prep I mostly go 120, 340, 400 or 600, then 0000 steel wool. But I HATE working with steel wool and wear a mask when doing so as you can see the steel dust floating in the air. When possible I use my Foredom hooded ventilator, but it only accommodates small work pieces.I see an interest in the thread, and I want to thank you all who participated. But... how many of us actually know what is the sandpaper made of and how to choose the correct one for a given job? Stay tuned and you will have a chance to learn, thanks to WIKI!!
Sandpaper, also known as glasspaper, is a heavy paper with abrasive material bonded to its surface. Sandpaper is part of the "coated abrasives" family of abrasive products. It is used to remove small amounts of material from surfaces, either to make them smoother (painting and wood finishing), to remove a layer of material (e.g. old paint), or sometimes to make the surface rougher (e.g. as a preparation to gluing).
The first recorded instance of sandpaper was in 13th-century China when crushed shells, seeds, and sand were bonded to parchment using natural gum. Sharkskin was also used as a sandpaper. The rough scales of the living fossil Coelacanth are used by the natives of Comoros as sandpaper. Boiled and dried, the rough horsetail is used in Japan as a traditional polishing material, finer than sandpaper.
Sandpaper was originally known as glass paper, as it used particles of glass. Glass frit has sharp-edged particles and cuts well, sand grains are smoothed down and do not work well like sandpaper made from glass. Cheap counterfeit sandpaper has long been passed off as true glass paper; Stalker and Parker cautioned against it in the 17th century. Glass paper was manufactured by John Oakey's company in London by 1833, who had developed new adhesive techniques and processes, enabling mass production. A process for making sandpaper was patented in the United States on June 14, 1834, by Isaac Fischer, Jr., of Springfield, Vermont.
In 1921, 3M invented a sandpaper with a waterproof backing, known as Wetordry. This allowed use with water, which would serve as a lubricant to carry away particles that would otherwise clog the grit. Its first application was automotive paint refinishing.
Material Materials used for the abrading particles are:
Sandpaper may be "stearated" where a dry lubricant is loaded to the abrasive. Stearated papers are useful in sanding coats of finish and paint as the stearate "soap" prevents clogging and increases the useful life of the sandpaper. The harder the grit material, the easier the sanding of surfaces like wood. The grit material for polishing granite slab must be harder than granite. Later abrading surfaces include long-life stainless steel sanding discs. Sandpapers can also be open coat, where the particles are separated from each other and the sandpaper is more flexible. This helps prevent clogging of the sandpaper. The wet and dry sandpaper is best used when wet.
- Flint: no longer commonly used
- Garnet: commonly used in woodworking
- Emery: commonly used to abrade or polish metal
- Aluminum oxide: perhaps most common in the widest variety of grits; can be used on metal (i.e. body shops) or wood
- Silicon carbide: available in very coarse grits all the way through to microgrids, common in wet applications
- Alumina-zirconia: (an aluminium oxide–zirconium oxide alloy), used for machine grinding applications
- Chromium oxide: used in extremely fine micron grit (micrometer level) papers
- Ceramic aluminum oxide: used in high-pressure applications, used in both coated abrasives, as well as in bonded abrasives.
View attachment 407726
View attachment 407727
Thank you and enjoy
I've started using purple abrasive, also from 3M, non clogging.what brand of sandpaper you are using? Also, are you talking about contact cement glue? Similar to this?
View attachment 407387
I use pink sandpaper made by 3M, and one with cloth on back by Kingspor