Typical hull planking strips (2nd layer) are 5mm wide and 0.6mm thick. These bend readily in one plane but any attempt to bend them 'sideways' results in kinks or breakage. When laid on a boat hull and allowed to follow their natural bend they tend to turn up and converge at the bow. Many tracts and video clips offer solutions to this problem. The principal ones seem to be:
1: spread out the planks round the fatter bulkheads and fill the gaps with shaped pieces - usually pointed at the ends.
2: on the upper part of the hull taper the planks and allow them to run from stem to stern. On the lower part use shorter planks that are allowed to turn up and are truncated where they meet the upper planks.
Token examples of these methods are illustrated below with extracts from OcCre kit instructions
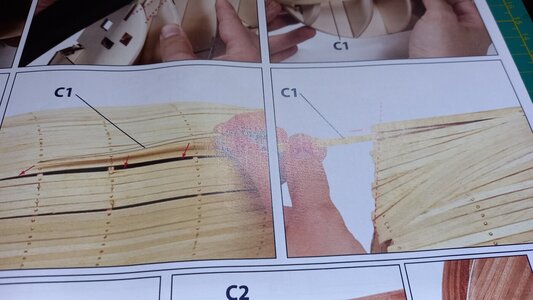
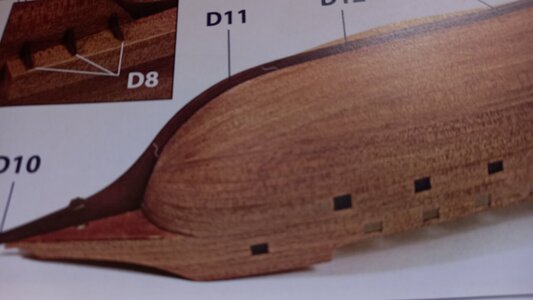
The Master Korabel Phoenixx kit (that I have almost completed) uses a different solution. Rather than supply planking strips the planks are laser cut from a sheet and shaped to counter the tendency to turn up at the bow. The following picture from the instruction manual illustrates the principle.
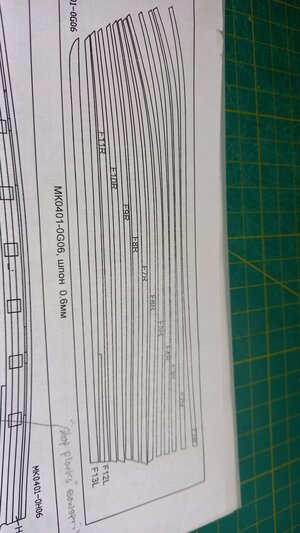
When applied to the hull frames the joints between the planks run parallel to the keel.
Looking at arbitrary website pictures of real wooden carvel planked boats it appears that tis would be the norm. Planks are shaped or steam bent achieve this.
I am about to start on an OcCre model of Revenge and I fancy trying this option as a change. I have bought some 1mm thick walnut sheet from which I hope to cut suitably shaped planks.
There would appear to be two approaches to creating these: empirical and theoretical.
For the empirical approach: assume a plank has somehow been laid with its edge parallel to the keel. A flexible strip can be paid alongside this at the midships section and go where it will towards the bow. The displacement above the fixed plank can be measured at various points along its length and a curve drawn through them. Similar measurements to to its bottom edge can be taken to complete a curved plank design. In the following image the pale plank runs parallel to the keel; the brown plank follows its will.
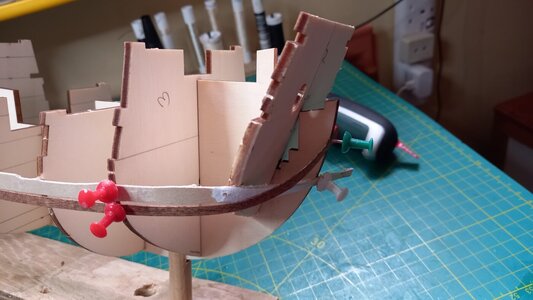
For a theoretical approach I have written a Mickey Mouse computer program. Input data is a set of points round the edge of each bulkhead. Each point (x,y,z) is defined by its height above the keel (Y) and the half width of the bulkhead at that height (X). Z is the distance of the bulkhead from the foremost part of the stem. Simple quadratic fitting of any three consecutive points around the bulkhead or along the edge of a 'deck' allow interpolation to any point on the hull.
In the following photo the upper part is a computer screen image of two 'decks' at 60 and 54 mm above the keel. At the top of the screen is a tentative outline of a plank that will follow the gap between the decks.
In the foreground is a print of this plank (in two parts 'cos I don't have an A3 printer) pasted on to a thin sheet of plywood.
Included for interest is a cross-section at bulkhead 6 which I printed and cut out to compare with the actual bulkhead. It was a reasonable fit.
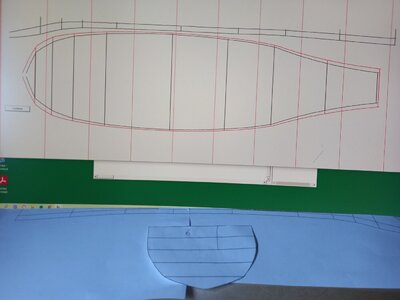
I have roughly cut the plywood plank and temporarily tacked it to the bulkheads. The top edge seemed to maintain the correct, constant height above the bottom of the keel.
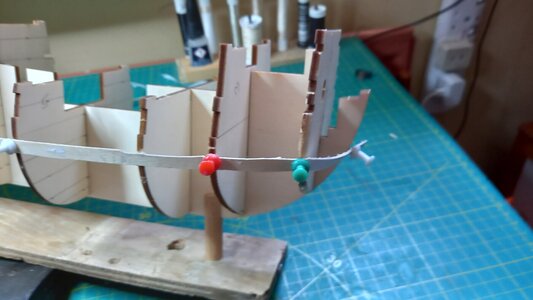
This is a work in progress. The task of using an electric scroll saw to to cut a plank required little more effort than that needed to taper a planking strip in conventional planking or to cut pointed inserts. I should be able to cut the port and Starboard pairs simultaneously.
I shall probably do the first layer planking the old fashioned way and try shaped planks for the second layer. I will get my program to revise the input data points to allow for the presence of the first layer planks. 1.5mm or 2mm thick probably.
The program may have some auxiliary uses such as designing working cradles or extra bulkheads
I shall report progress - or failure if that is the case.
1: spread out the planks round the fatter bulkheads and fill the gaps with shaped pieces - usually pointed at the ends.
2: on the upper part of the hull taper the planks and allow them to run from stem to stern. On the lower part use shorter planks that are allowed to turn up and are truncated where they meet the upper planks.
Token examples of these methods are illustrated below with extracts from OcCre kit instructions
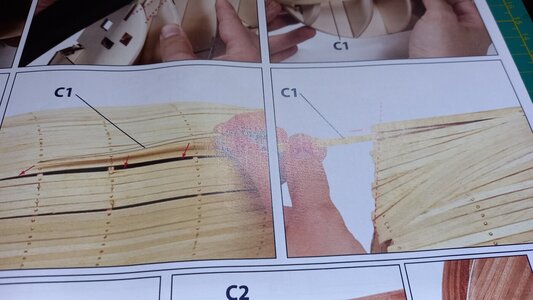
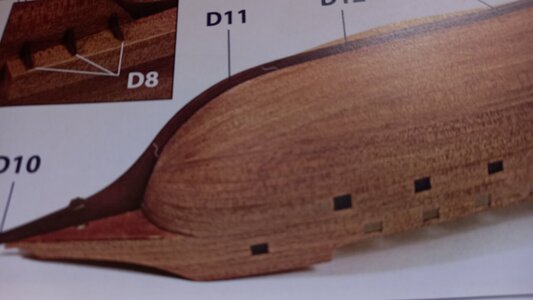
The Master Korabel Phoenixx kit (that I have almost completed) uses a different solution. Rather than supply planking strips the planks are laser cut from a sheet and shaped to counter the tendency to turn up at the bow. The following picture from the instruction manual illustrates the principle.
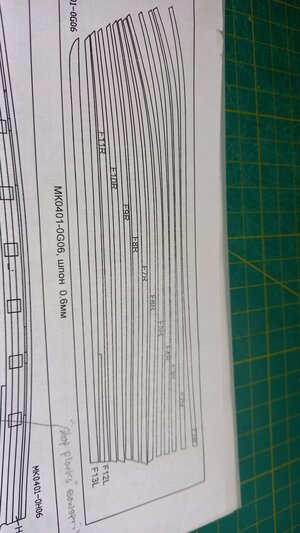
When applied to the hull frames the joints between the planks run parallel to the keel.
Looking at arbitrary website pictures of real wooden carvel planked boats it appears that tis would be the norm. Planks are shaped or steam bent achieve this.
I am about to start on an OcCre model of Revenge and I fancy trying this option as a change. I have bought some 1mm thick walnut sheet from which I hope to cut suitably shaped planks.
There would appear to be two approaches to creating these: empirical and theoretical.
For the empirical approach: assume a plank has somehow been laid with its edge parallel to the keel. A flexible strip can be paid alongside this at the midships section and go where it will towards the bow. The displacement above the fixed plank can be measured at various points along its length and a curve drawn through them. Similar measurements to to its bottom edge can be taken to complete a curved plank design. In the following image the pale plank runs parallel to the keel; the brown plank follows its will.
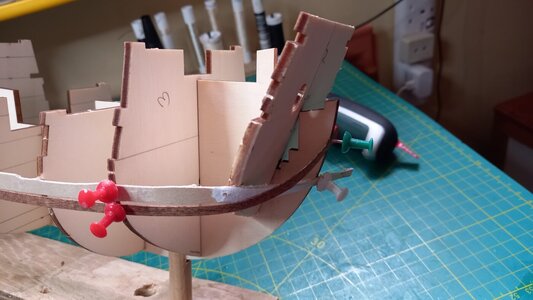
For a theoretical approach I have written a Mickey Mouse computer program. Input data is a set of points round the edge of each bulkhead. Each point (x,y,z) is defined by its height above the keel (Y) and the half width of the bulkhead at that height (X). Z is the distance of the bulkhead from the foremost part of the stem. Simple quadratic fitting of any three consecutive points around the bulkhead or along the edge of a 'deck' allow interpolation to any point on the hull.
In the following photo the upper part is a computer screen image of two 'decks' at 60 and 54 mm above the keel. At the top of the screen is a tentative outline of a plank that will follow the gap between the decks.
In the foreground is a print of this plank (in two parts 'cos I don't have an A3 printer) pasted on to a thin sheet of plywood.
Included for interest is a cross-section at bulkhead 6 which I printed and cut out to compare with the actual bulkhead. It was a reasonable fit.
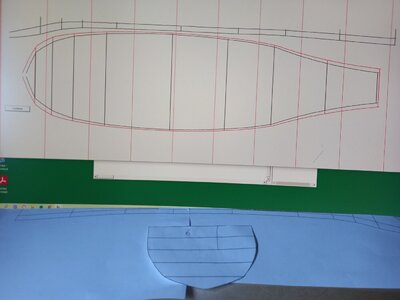
I have roughly cut the plywood plank and temporarily tacked it to the bulkheads. The top edge seemed to maintain the correct, constant height above the bottom of the keel.
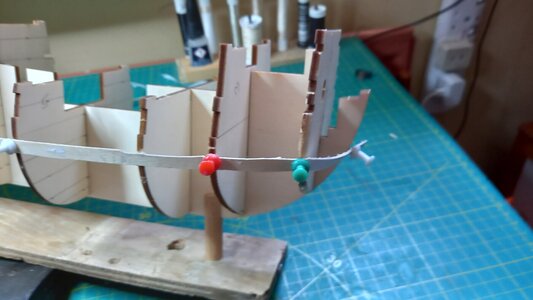
This is a work in progress. The task of using an electric scroll saw to to cut a plank required little more effort than that needed to taper a planking strip in conventional planking or to cut pointed inserts. I should be able to cut the port and Starboard pairs simultaneously.
I shall probably do the first layer planking the old fashioned way and try shaped planks for the second layer. I will get my program to revise the input data points to allow for the presence of the first layer planks. 1.5mm or 2mm thick probably.
The program may have some auxiliary uses such as designing working cradles or extra bulkheads
I shall report progress - or failure if that is the case.