Ahoy! Shipmates! I have just given my DB250 a 'face-lift' by adding a cross-slide tool post that can be adjusted to produce straight & tapered parts. The parts came from cannibalising a 'carppy' China micro 'lathe'. The angle adjustment is achieved by slackening the clamping thumbscrew then turning the adjusting knob to the desired amount of taper. Feeler gauges can be used to set the taper for repeat production. The spars just need a bit of sanding to clean-up, works perfectly for Le Superbe's yards. I can also produce pulley block sheaves from brass.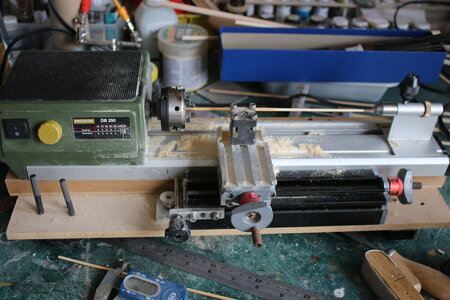
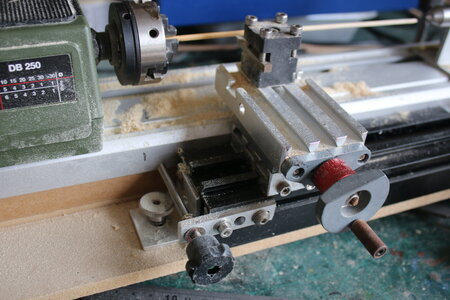
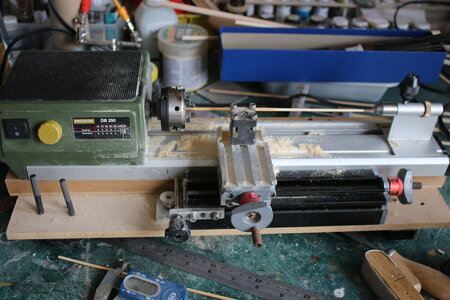
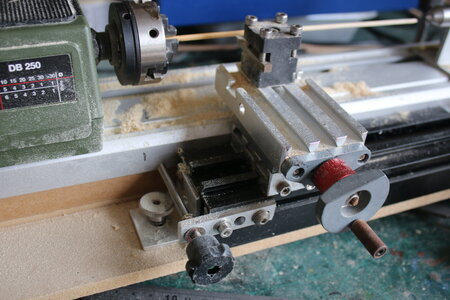