I have a Proxxon thicknesser which is used almost daily. It is good but has 3 major drawbacks:
Minimum thickness is only 1.3mm and it chews up short or irregular pieces. (Double-sided tape doesn't work for me). Also it can’t “match” an outer curve - very useful when making beams.
I’ve gazed enviously on the Bryne’s offering and recently someone offered (used) something similar. The asking price was very fair, but shipping and tax multiplied cost fourfold or more.
I decided to adapt some previous ideas and underused equipment.
I remembered a sanding drum I’d made from an old rolling pin, and some sleeveless sanding drums that I’d bought for more accurate work.
I had bought a sort of lathe system, with 2 motors and chucks and a 3rd non motorised chuck.
The basic plan was to use this as a base, attach a hinged platform adjusted by a screw system.
I started with some metal plates 1.75mm thick, which I cut to size and attached the hinges with epoxy-which didn’t hold. I changed to 4mm perspex, breaking a couple of corners when drilling holes for the small nuts and bolts that I used to attach the hinges. So I ended with an upper perspex and lower metal plates.
The (metal) elevating screws were set into some handles which were cut off some plastic screws.
I know it looks like Heath Robinson on LSD, but it works !
(I thank my wife for donating the rolling pin)
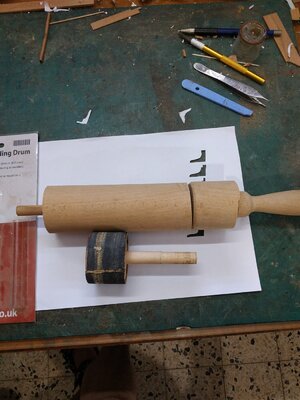
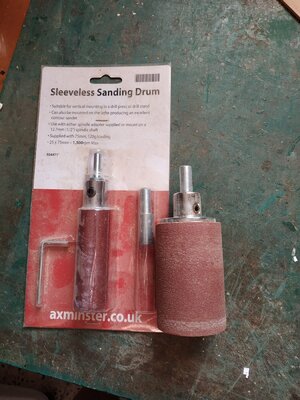
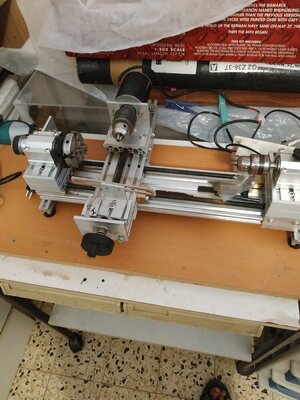
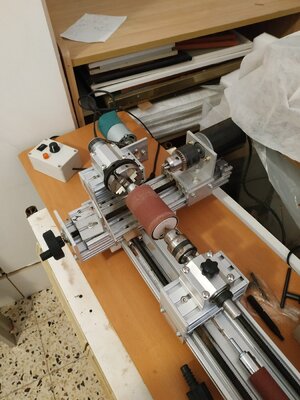
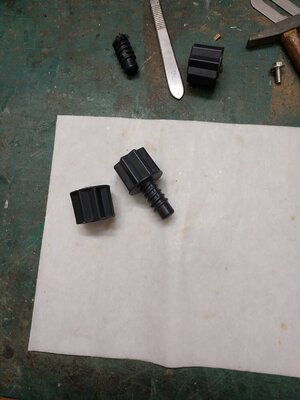
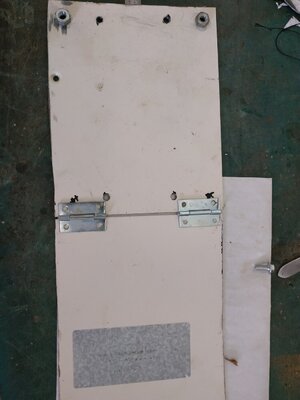
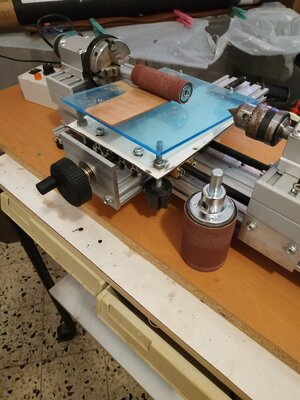
Minimum thickness is only 1.3mm and it chews up short or irregular pieces. (Double-sided tape doesn't work for me). Also it can’t “match” an outer curve - very useful when making beams.
I’ve gazed enviously on the Bryne’s offering and recently someone offered (used) something similar. The asking price was very fair, but shipping and tax multiplied cost fourfold or more.
I decided to adapt some previous ideas and underused equipment.
I remembered a sanding drum I’d made from an old rolling pin, and some sleeveless sanding drums that I’d bought for more accurate work.
I had bought a sort of lathe system, with 2 motors and chucks and a 3rd non motorised chuck.
The basic plan was to use this as a base, attach a hinged platform adjusted by a screw system.
I started with some metal plates 1.75mm thick, which I cut to size and attached the hinges with epoxy-which didn’t hold. I changed to 4mm perspex, breaking a couple of corners when drilling holes for the small nuts and bolts that I used to attach the hinges. So I ended with an upper perspex and lower metal plates.
The (metal) elevating screws were set into some handles which were cut off some plastic screws.
I know it looks like Heath Robinson on LSD, but it works !
(I thank my wife for donating the rolling pin)
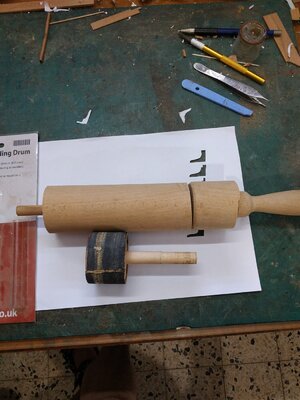
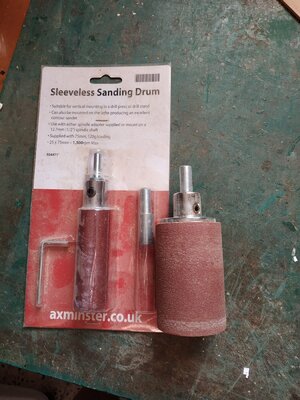
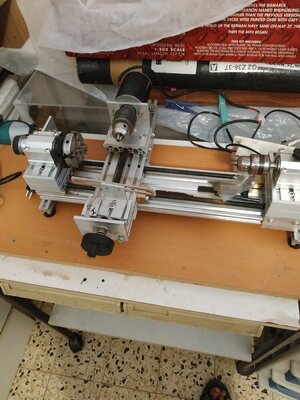
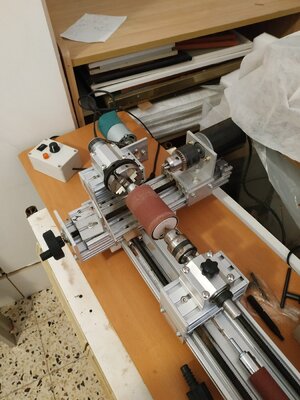
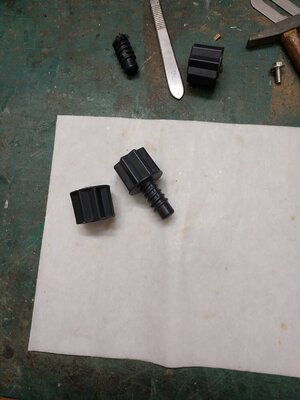
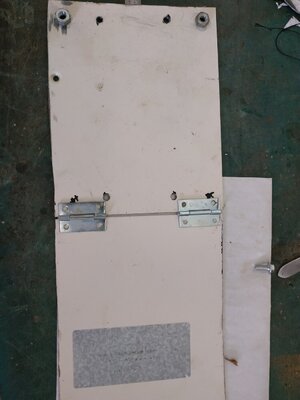
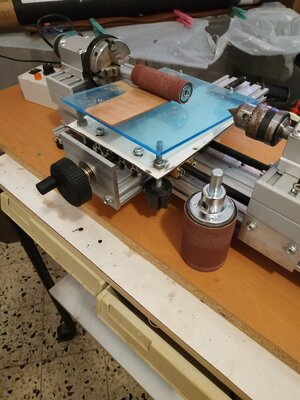