Well,
The previous thread I was reading about the motor / Rope Walk encouraged me to at least try and build one. I found a pretty good electric shaver and dismantled it some. Just enough to get to the bare post. I was able to machine using a lathe and a mill to make adapters for the shavers post. The holes were of very close tolerances that I will be able to just use Red Locktite to bond them into place. Below are a few pics so far. I hope that I can keep this up to come up with a finished product that works. I plan to wire up a remote switch so I do not have to reach up to turn it on. Mine will be about 8 foot to the Ceiling.
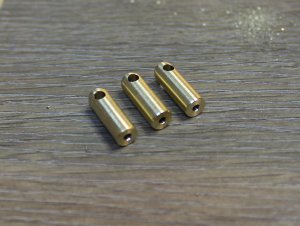
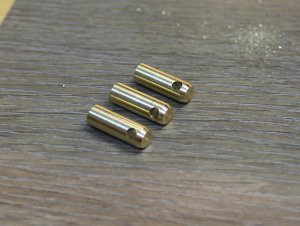
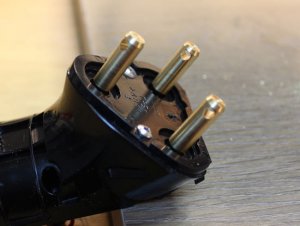
The previous thread I was reading about the motor / Rope Walk encouraged me to at least try and build one. I found a pretty good electric shaver and dismantled it some. Just enough to get to the bare post. I was able to machine using a lathe and a mill to make adapters for the shavers post. The holes were of very close tolerances that I will be able to just use Red Locktite to bond them into place. Below are a few pics so far. I hope that I can keep this up to come up with a finished product that works. I plan to wire up a remote switch so I do not have to reach up to turn it on. Mine will be about 8 foot to the Ceiling.
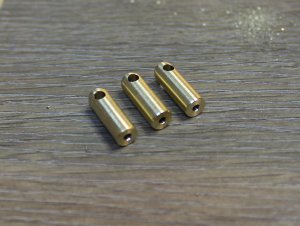
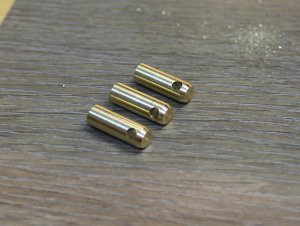
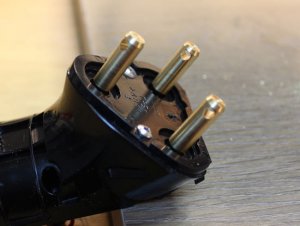